BTI build global reputation from small town Ontario
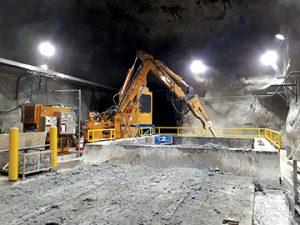
A BTI rockbreaker at work. CREDIT: BREAKER TECHNOLOGY
From the parking lot at Breaker Technology Ltd.’s head office in Thornbury, Ont., a two-hour drive from Toronto, you can see right down to the vivid blue waters of Georgian Bay. It’s been from this location in a picturesque vacation town that the company has built a reputation as one of the world’s foremost manufacturers of rockbreaker systems for the mining sector.
“We’re known around the world as one of the leading suppliers of this product and it goes from small right through to the really big ones and all different types of applications,” says Terry McKague, Breaker Technology’s director of sales, International and Canada.
Rockbreakers are used at both underground and open pit mines to break down oversized ore so it can enter the crusher.
However, Breaker, also known as BTI, makes much more than just rockbreakers.
It also manufactures a complete line of mobile equipment, including scalers, ANFO loaders, remixers and Mine Runner vehicles for various production and support applications. The company was founded as JMG in 1958, when three mining professionals – two metallurgists and a former mining executive with a cottage in Thornbury – started their own business manufacturing replaceable drill parts for the industry. Just five years later, the company was bought by Teledyne, a U.S. company.
It was in the mid-1970s that the company (then Teledyne Canada Mining Products) became the first to sell purpose-built rockbreaker systems to break up oversized ore that wouldn’t fit through the grizzly stations covering the ore passes. Working closely with mining companies, Breaker developed the first purpose-built rockbreaker and found a ready market.
Rockbreaker Systems are still a key part of ore flow facilitation and BTI’s clients include some of the largest mines in the world.
“These mines can’t have any down time,” says McKague. “If that machine goes down it costs them a lot of money.
So they’ve come to know our product as one of the most reliable to keep running day in, day out for years.”
In 1999, NASDAQ-listed Astec Industries bought Teledyne Canada Mining Products and the company was renamed Breaker Technology, after its best-known product. Since then, it’s been a part of Astec’s Aggregate and Mining Group. Astec, which also has infrastructure and energy groups, has 19 companies in total, each retaining its own distinct brand and identity.
Led by President Don Sissons, BTI currently employs around 160 people, including 20 in the U.S. Offices in the Cleveland suburb of Solon, Ohio, and in Riverside, Calif., provide sales and service support stateside, while the main Thornbury office serves Canadian and international clients.
More than rockbreakers
To date, BTI has completed around 3,000 installations of rockbreaker systems, including the world’s biggest rockbreaker, the TRX, which stretches out an impressive 64 ft. and weighs over 100,000 lb. BTI developed the TRX in 2013 for the Iron Ore Company of Canada’s Labrador City operations. Other notable clients include Codelco’s El Teniente underground mine and its Chuquicamata open pit mine in Chile.
In addition to rockbreaker systems, BTI has a long history making scalers – equipment that’s used to dislodge loose rocks in underground mine headings after blasting to lower the risk of falling rocks. It made the first one in 1981 with the help of a Canadian government grant and ended up selling three to a mine in Peru. (Incidentally, two of those original scalers – now rebuilt – are still working.) Until recently, BTI’s scalers were large, heavy, and on the expensive side.
While it still has a few dedicated customers who keep coming back for this type of machine, the company recognized it couldn’t break into new markets with the existing product.
Finding inspiration from a client in Peru who had built their own homemade machine with increased flexibility, in 2012, BTI introduced its RMS 18 scaler. The machine offered enhanced flexibility and extremely high availability.
However, it was still a little too big, so in 2016, BTI came out with the ScaleBOSS 3D Scaler – a machine that’s smaller and cost effective for smaller headings. It also offers improved flexibility with a 5-axis boom and operate up to 5.5 metres.
“We’re finding that it’s more productive, more reliable and more comfortable for both the operator and maintenance personnel,” says McKague, who joined BTI in 1988.
The machine scales up two times faster than any other scalers, has faster controls, 5-axis positioning of the hammer, excellent operator visibility, and ergonomic design that reduces operator fatigue.
Another product that’s unique to BTI is its Mine Runner vehicles, first introduced four years ago. The all-purpose mining vehicles can carry much more than trucks typically used at mine sites – 6,000 lb. in comparison to 900 lb.
“A lot of people think that it’s too large for their environment and they don’t realize that it has a very tight turning radius,” says BTI’s marketing co-ordinator, Julie Simmonds. “It’s very agile.”
A new version with an extended wheel base will be unveiled shortly. The new Mine Runner will have the ability to carry even more weight, with an environmentally controlled ROPS / FOPS (roll over and falling object protection systems) passenger cabin that can carry up to 15 people at once (up from 8).
A second generation of the Scale- BOSS is also in the works, Simmonds says. “Right now, it’s good for the 3- to 5-metre heading. The next model will be designed for 4-to-7 metre headings while still keeping it compact and flexible.”
Focus on quality
On a tour of BTI’s manufacturing floor in June, Terry McKague notes that BTI manufactures as many parts and components as possible in-house – first to ensure quality control and second, to minimize delays on new orders.
As an ISO certified company since 1998, BTI has a quality management system equipped to meet the high standards required by large mining and engineering companies.
“Often, the large mining companies and the engineering firms will ask us to hold at certain points of the manufacturing process so they can send their own third party inspectors to come in and check our quality records and check the products,” McKague says.
“Our system… marries up really well with what they’re asking for. If we didn’t have that system in place, we would not be able to build equipment for large mines and large engineering firms.”
BTI uses lean manufacturing principles, such as value stream mapping, to focus energy and resources into two different streams – the rockbreaker system line and mobile equipment manufacturing.
Each stream has dedicated engineers, manufacturing experts and purchasing experts.
‘It’s good to be busy’
Like any OEM, BTI’s business ebbs and flows with industry fortunes. But after a couple of slow years in 2014-16, orders have picked up, says product manager John Wittenberg.
“The North American economy is doing rather well,” he says, estimating that business in the U.S. and Canada is up substantially. “Our international business in certain countries has almost doubled.”
Wittenberg says the company is as busy now as it was in 2012-13 – a very good year for BTI.
“We’re back up near peak,” he says.
“It’s good to be busy.”
With that, however, comes the challenge of longer lead time times for parts that aren’t manufactured in house.
“Our suppliers are seeing extended lead times – what used to be stock for a lot of components seems is now back ordered with extended lead times,” Wittenberg says, extended the lead times for engine, drive line and hydraulic components are hardest hit.
Innovation
An increasing number of underground rockbreaker systems that BTI sells are operated remotely via the company’s Breaker Intel Systems, a long distance remote system. BTI supplies an array of scalable long distance control systems with single or multi-boom control combined with integrated low latency video monitors. As the company steps towards automation, further enhancements include position feedback systems for site specific collision avoidance and park/deploy functions improved operator experience and cycle times.
And for what it’s already achieved with its rockbreakers’ remote operation capabilities, BTI recently received the 2017 Science and Technology from the China Gold Association after it was nominated by client Shandong Gold.
“It’s the innovation that I love because when we come out with these new machines, we’re taking the existing problem at a mine and trying to solve it with something that’s not available – taking the mining industry to a new level,” McKague says.
Comments