Bridging the gap: Training considerations for transitioning from open pit to underground mining
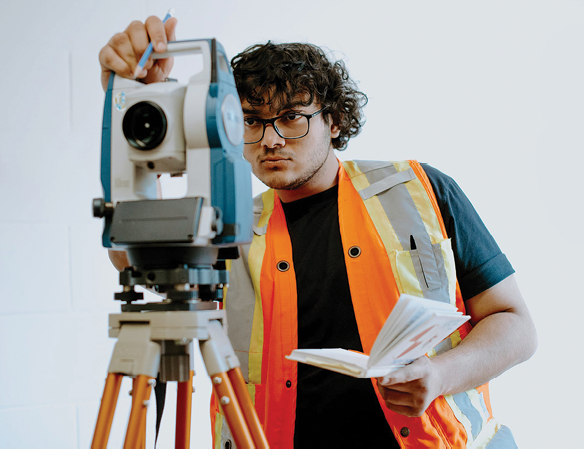
As some mines evolve from open pit to underground operations, a fundamental transformation occurs in the skills and knowledge required from the workforce. This transition brings new challenges necessitating specialized training to ensure worker safety, operational efficiency, and overall productivity. With distinct underground environments and advanced technologies like automation and remote systems, a comprehensive approach to workforce development is critical. Training that emphasizes both technical expertise and safety is essential to manage these changes effectively and sustain mining operations. While much of the discussion around transitioning from open pit to underground mining tends to focus on the technical aspects, such as equipment and operational procedures, the equally important human resource shift often receives less attention. Addressing both the technical and human elements is key to a sustainable shift in mining practices.
Training considerations in this context must address the distinct challenges of underground environments, such as confined spaces, reduced visibility, and heightened risks of rock falls or equipment failure. Workers accustomed to the open pit setting need to learn how to navigate the unique hazards posed by underground mining, including the need for enhanced ventilation, ground control, and emergency evacuation procedures. Additionally, specialized equipment used underground, such as low-profile vehicles and drilling machinery, requires targeted training on operation and maintenance. Emphasis should also be placed on adopting new technologies, like autonomous systems and remote monitoring, which are increasingly integrated into underground mines. Training programs must therefore not only focus on technical skills but also on fostering a culture of safety, continuous learning, and adaptation to emerging technologies. Furthermore, leadership and communication training have become crucial in the underground context, where coordination and timely decision-making are vital to maintaining a safe and productive work environment. In sum, a comprehensive training strategy is pivotal for a smooth transition, ensuring that the workforce is well-equipped to meet the operational and safety demands of underground mining.
A smooth transition from open pit to underground mining relies not only on comprehensive training programs but also on a strategic decision about when to make the shift. While training equips workers to handle the unique challenges of underground operations, determining the right time for the transition involves a deeper evaluation. Two common approaches guide this decision: maximizing the open pit mine’s potential before transitioning or conducting a cost analysis to determine when underground mining becomes more financially viable. Both approaches must consider workforce readiness and operational demands.
In underground mines, several job functions are unique because of the specific challenges of working below the surface. Ground support technicians are crucial for stabilizing rock formations using bolts and mesh. Ventilation engineers design systems to ensure proper airflow, maintain breathable air, and manage hazardous gases. Underground tradespeople like electricians and mechanics handle the maintenance of equipment and infrastructure installations in confined spaces. Underground drill operators drill vertical shafts for ventilation and ore transport, while underground surveyors map and measure tunnels to ensure accurate excavation and safe mine planning, critical for navigating underground environments. To make a shift to the underground easier for workers into these specialized roles, comprehensive reskilling programs are essential, equipping open pit workers with the technical skills needed for underground environments while minimizing workforce disruptions.
Upskilling and reskilling open-pit mining staff to work in underground mines is crucial for sustaining local economies, as the potential for job losses during this transition poses a significant risk to communities dependent on mining. Without adequate training programs, many workers could face unemployment, leading to economic decline in regions where mining serves as a primary source of income. This not only affects individual livelihoods but also puts pressure on local businesses and services that rely on the spending power of mining employees. By investing in comprehensive training, companies can retain their workforce, reduce layoffs, and ensure continued economic stability. Furthermore, skilled workers who are adaptable to underground operations become valuable assets, helping to future-proof the workforce and promote long-term growth in mining regions. This proactive approach not only benefits the company but can also preserve the social fabric of the community, fostering resilience in the face of industry shifts. In service of this goal, colleges and training centres play a crucial role in offering the necessary training to fill this skills gap and support a successful workforce transition.
Canada’s college system is well-equipped to support the upskilling of workers transitioning from open pit to underground mining through its diverse corporate training offerings. Corporate training offers industry access to resources and programming typically used to train post-secondary students. Whether through short-term, targeted courses or longer-term, multi-course programs, colleges can support the training needs of the mining sector. In addition to specialized education in key underground technical areas like ground control, surveying, and ventilation engineering, colleges can provide cutting-edge courses in topics ranging from data analytics and artificial intelligence (AI) as well as electric and autonomous vehicle maintenance. With the rise of digital technologies and the shift towards electrification in underground mines, these programs equip workers with vital skills for analyzing operational data and maintaining systems. This ensures that the workforce is not only technically proficient in traditional underground roles but also adept at handling modern, technology-driven mining operations. By addressing both technical services and new technological competencies, corporate training centres help create a highly skilled, adaptable workforce capable of meeting the demands of modern underground mining.
Successfully transitioning a mine from open pit to underground operations hinges on the ability to upskill and reskill the existing workforce. By investing in targeted training programs, mining companies can ensure that workers are well-prepared for the demands of underground environments. This not only prevents job losses but also supports local economies, enhances safety, and fosters long-term stability in mining communities. A well-trained workforce is the cornerstone of a safe, efficient, and sustainable transition.
Steve Gravel is the manager of the Centre for Smart Mining at Cambrian College.
Comments