Autonomy lessons from early adopters
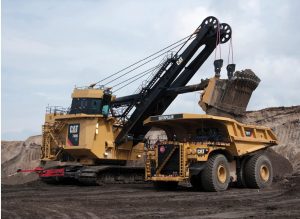
Cat 7495 HF Shovel loads Cat 797F truck in an oilsands mine. Oilsands operations have been early adopters of automation. CREDIT: FINNING
Autonomous and semi autonomous applications were terms once used to describe mines of the future, but that future is now. The industry as a whole is sold on the precision, efficiency and productivity benefits of autonomy, although we are still seeing a more conservative approach to adoption in Canadian mines.
Making the shift to semi-autonomous or fully autonomous applications is complex, particularly in remote locations. It often involves a complete redesign of the mine and an overhaul of existing processes. We’ve learned from early implementers that the biggest challenge isn’t the technology itself but the impact it has on people, process and technology. To be effective, a significant amount of time needs to be spent on change management with a strong focus on all three components. When working together, it can lead to an increase in productivity and improved bottom line.
A change management approach
Autonomous trucks are programmed to operate largely on their own, delivering on their assigned tasks, only modifying their path to accommodate obstacles. They communicate with a central control system that is managed remotely by an operator. The truck can easily drive autonomously from point A to point B, or stop at the push of a button. It is 100% accurate and completely predictable. The key variable is the human component.
In mining, where the stakes are high and the way of working has been the same for so long, autonomous implementation can often mean a significant adjustment. The biggest challenge is the organization’s ability to manage the resistance to change.
Incorporating a remote-control dozer or two into your existing operating practices is a change; but implementing a full autonomous haulage system takes major adjustments and often calls for a complete redesign of mining operations. You’ll need to reconfigure your basic operating procedures and – most important – get everyone on board with the program from the start. This involves a commitment to change management and a willingness to adjust to a ‘new normal’ around your autonomous system. But the benefits far outweigh the risks and the right technology dealer can help with this process – not only the implementation of the technology but looking at the skills and competencies of existing operators, risk mitigation and developing greater confidence in the change process and benefits.
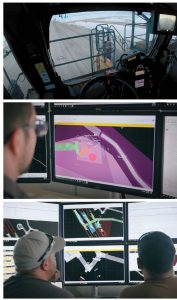
Top left: An autonomous cab in the oilsands.
Middle and bottom left: Autonomous touch screens. CREDIT: FINNING
Collaboration is key
Mines are a highly dynamic, complex environment and on any given day there are hundreds of things to deal with – from people, processes, costs, equipment and terrain to weather and material type. The first step is always identifying the problem to be solved, then you can determine the solution to address it and whether a technology solution is the right answer.
An autonomous mine site involves a lot more than autonomous machines. While the technology exists to build a truck that can navigate a haul road, it has to be able to work as part of a mine site system – interacting with every piece of equipment and person on site. Partnering with an equipment technology dealer who understands your business is key – they can help identify the infrastructure that needs to be in place, what technology is required and any gaps that may exist. This is an integrated approach, a collaborative effort between the mine management team and the equipment technology provider, using technology as a strategic tool to address safety concerns, increase haulage and productivity and lower your cost per ton.
With an unpredictable market and budgets tighter than ever before, converting to autonomous operations is a big commitment. But as more companies implement autonomous systems, the cost of development and the application will become far more cost-effective. This symbiotic relationship works in the technology developer’s favour as well – the more the technology is being used and the more feedback received, the greater the adaptions to the technology, resulting in an even more effective system to support mining operations.
The evolution of roles
Autonomy allows equipment to operate 24/7 increasing efficiencies on site and totally eliminating downtime associated with breaks and shift changes. The value is undeniable and the benefits are obvious – greater productivity and increased safety for workers. So more focus needs to be placed on addressing what it will mean for jobs on the mine site of the future.
There will always be a human element to operating mines and as the industry enters into this new era of autonomy, jobs aren’t necessarily being eliminated, but roles are evolving with the technology and skill set required. Technicians and data specialists who understand operational control, predictive maintenance and mine planning will be in high demand. Workers will need to be highly skilled in technology, computer science and engineering. Even the responsibility of the mining manager will shift – they will still need to understand general mining operations but they will also need to be well versed on autonomous technology systems.
Recruitment is an essential part of the strategy. Labour shortages have long been an industry concern – many plan to retire in the coming years and there is a small pool of talent highly skilled and educated in sophisticated technology. New workers may understand the technology but they won’t necessarily have an understanding of the mining environment. This experience, knowledge and insight cannot be learned by operating equipment remotely from an office. This next generation will need to tap into the knowledge from those who have decades of experience in the industry. Companies can also overcome concerns of role changes by offering training and education to transition more experienced workers into new roles.
The mines of the future will have an expansive range of needs and roles – they’ll need both the experience and insight from on the ground and the skill level and expertise to manage the technology aspects of the business.
Reap the benefits and overcome the hurdles of change
The successful implementation of these new technologies requires changes to every part of the mining business. However, people and process remain the biggest challenge, no matter how smart the technology is. Here are a few ways companies can help remove the barriers to implementation.
- Identify technology champions: Technology champions can lead by example and reinforce the importance of change. When there is someone on site committed to maintaining forward progress, it’s harder to fall back into outdated practices that no longer support the operation.
- Leverage education and training opportunities: When it comes to managing change within an organization, it is important to offer education and training programs. This will help prepare your people for autonomous implementation and can make a significant difference with respect to profitability, safety and extending equipment life.
- Consider a staged approach: With a staged approach, participants are brought into the discussion early before full autonomy is deployed. While full autonomy is the end goal and can result in seeing the benefits sooner, a semi-autonomous approach may be easier to start with. It eliminates many manual tasks, improving safety and productivity while gaining the trust and confidence of employees through adaptation. Keep in mind, there are no semi-autonomous trucks, so with this approach it could also take longer to see the full benefits of the technology.
- Focus on the safety benefits: Operators not familiar with autonomous technology may feel uneasy seeing a huge haul truck driving through a site without a driver. Sensor technology is now so advanced that autonomous trucks sense even the smallest of hazards and react instantaneously. It’s important everyone in the company understands that a switch to autonomous systems can have a huge impact on improving safety – removing workers from harmful situations. Automated equipment including haul trucks can also mitigate the danger of driver fatigue and boost the efficiency of the whole operation.
- Help workers get comfortable with the changes: Mine sites need to assess existing processes, pick the ones that work and keep them in place until the team gets comfortable with the changes. When the time comes, it will be easier to transition to the new processes that will further improve operations.
A proactive approach helps guarantee success
Autonomy is a game changer in terms of improved efficiencies and productivity. Canadian mining companies are beginning to see autonomous technologies as a way to provide a safer and more proficient operation. The real benefits lie in a successful implementation, and when done right can add immense value – providing huge gains in productivity and cost reduction, offering improved safety, efficiency, and a lower cost per ton.
To truly see business success, Canadian mines need to drive costs down and autonomy can help. In order to overcome the challenges of tomorrow, mining companies need to rethink the way they do business today, including the way they design, build and operate their mine. Working with the right equipment and technology dealer and making change management a priority can help companies successfully implement an autonomous system, gain substantial benefits in their operations and a significant advantage over their competitors.
Adam Brumwell is the director of autonomous solutions and mining technology for Finning Canada (www.finning.com/en_CA.html). Adam and his team are accountable for implementation and support of autonomous, semi-autonomous, grade control and fleet management systems for mining customers across Western Canada.
Comments
pat rich
I wish they would drop this 24/7 line. All mining equipment has to be maintained and refueled. All equipment needs to be inspected for damage, worn out tires , serviced. etc. Added to that is the computer operator running the unit: he needs to have coffee breaks, lunch, etc. Everyone dreams of 100% availability, but its a dream. Reality kicks in as equipment ages, meaning higher the hours, more down time.