Applying the 3Rs to mine ventilation
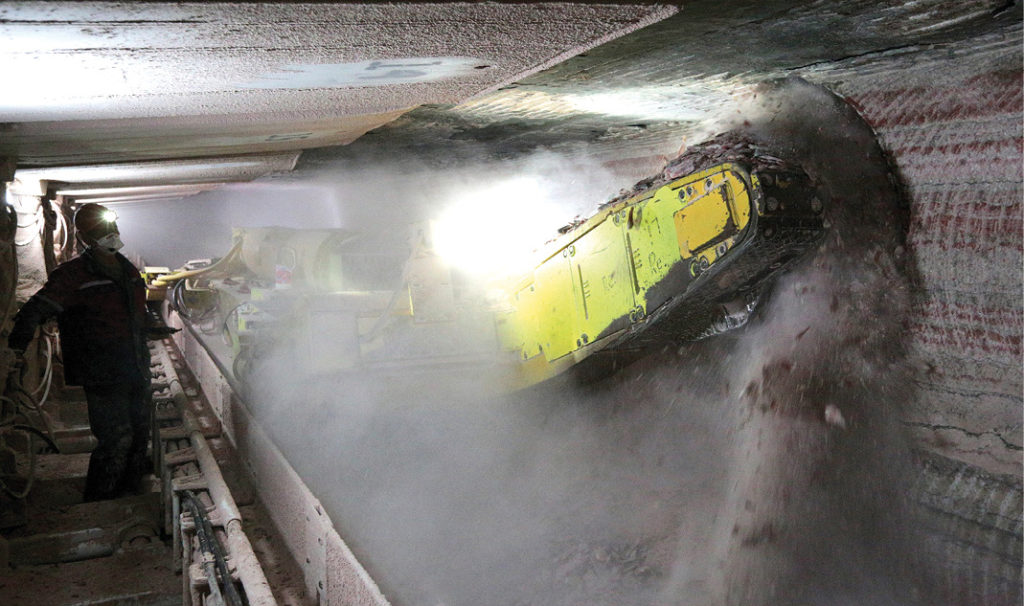
If you have ever been in an underground mine, you know how important ventilation is. Ventilation is essential to maintaining safe working conditions by providing adequate airflow to dilute contaminants and heat. In underground mines, ventilation can account for up to 50% of the total energy use. And, that percentage increases for deeper mines that also need cooling. With increased importance on sustainable mining and reducing greenhouse gas (GHG) emissions, how can we reduce a mine’s energy use on critical ventilation needs? Let us apply the 3Rs: reduce, reuse, and recycle to ventilation system design in underground mines.
REDUCE
Conventionally, in underground mines, the ventilation requirements have been driven by legislation. Regulations require ventilation to dilute diesel particulate matter, with additional ventilation provided as required for hot or gassy mines. Operating with higher-tier engines or installing a diesel particulate filter (DPF) will produce fewer diesel particulate emissions, requiring less ventilation. For example, Canmet will require 10.1 m3 per second of ventilation to be provided for a Tier 2 Caterpillar C11 engine, while the same engine with a diesel particulate filter will require only 5.29 m3 per second of ventilation. That is a reduction of almost half.
Going a step further and transitioning to an electric fleet will need much less ventilation. Diesel engines (through combustion) produce significant air contaminants and heat. But electric vehicles operate by an electric motor and do not produce any air contaminants. For an electric fleet in a non-gassy mine, the ventilation system needs to be designed for heat dilution and maintaining minimum velocities. Since the heat produced by an electric motor is much less than a diesel engine, the switch to an electric mobile fleet can result in a 40% reduction in ventilation demands.
Another way to reduce ventilation needs underground relates to being more efficient. Ventilation on demand (VOD) can be implemented to meet ventilation needs without over-ventilating during underground activities that do not require peak ventilation or in non-active mining areas. VOD systems adjust the primary ventilation provided underground based on the underground activities through variable frequency drives (VFDs) at the main fans. Airflow can then be distributed underground through automated louver regulators, with air quality stations monitoring the air flow and quality underground. The regulators can provide sufficient air, based on the equipment present, to maintain gas and heat levels at a threshold or based on a schedule. The savings from a VOD system are variable, in the range of 30% to 50%, based on the size and the ventilation strategy for the mine.
Reducing ventilation requirements underground will result in a direct reduction in the cooling/heating required, since less air will need to be conditioned. This will result in a significant reduction in the energy used to provide ventilation, as well as the associated ventilation infrastructure (raises, fans, electrical gear, etc.). Mine energy reduction is good for both owners and operators. It saves money, and it is good for the environment, as it creates fewer carbon emissions.
REUSE
Typically, in underground mines, we have limited options when it comes to reusing air. This is because we need clean air to minimize workers’ exposure to contaminants in the air and airborne dust. However, it is possible to reuse heat. Let us explore how to reuse waste heat to either heat or cool the mine.
In cold climates, ventilation air needs to be heated to prevent ice buildup on the ventilation airways. Ice can cause major damage to the mine services. The exhaust air from the underground ventilation system can preheat the intake ventilation air. When the exhaust air raise is close to the intake raise, an air-to-air heat exchanger can recover the heat. On the other hand, when the exhaust air release on surface is far from the intake air, an indirect heat exchanger is more cost-effective. This kind of heat exchanger typically uses glycol as a heat transfer medium.
In remote mines, gensets are routinely used for electricity generation. When the gensets are producing power, they also produce a significant amount of heat. This heat is much higher grade than the mine exhaust air, but similarly can be recovered through a glycol indirect heat exchanger to provide most of the heating required for the ventilation air.
In hot locations, where cooling rather than heating is required, and high-grade waste heat is available, an absorption chiller can be installed to provide chilled water for conditioning the ventilation air. Even though it sounds backwards, absorption chillers use heat instead of power to produce cooling. This means the system requires minimal power consumption for both pumping and the fans to operate the refrigeration system.
RECYCLE
For deep mines, a lot of the energy in operating the ventilation system is used to overcome the friction to deliver the air to the orebody and then exhaust it back to surface. In addition, when air is delivered to deep mines, the air heats because of the auto-compression at approximately 1°C per 100 m3. So, if we can clean and recycle the air underground, the system would need a lot less cooling (or heating in a cold environment) and power.
In non-gassy mines without diesel mobile equipment, recycling of the mine ventilation can be safely performed through controlled partial recirculation (CPR). This strategy uses a percentage of the exhaust air, cleaning and mixing it with the intake air. The air is typically cleaned through a spray chamber designed to remove airborne dust. The Taquari potash mine in Brazil has effectively used a CPR system for many years.
With the transition to mobile electric fleets and improvements in the ventilation monitoring and control systems, CPR systems could be implemented safely in more mines to recycle the ventilation air and significantly reduce ventilation requirements.
Striving to make ventilation more affordable and sustainable
Applying the 3Rs to ventilation system designs can help a mine reduce its energy use, and subsequently, its carbon footprint. These enhancements can result in lower operational costs as a result of needing less energy. It also means lower capital cost due to smaller ventilation and associated infrastructure.
When considering ventilation and cooling/heating options for underground mines, it is important to innovate and incorporate sustainable design practices. Through creative thinking, our mines can be ventilated affordably and sustainably.
Kim Trapani is a ventilation engineer with experience across the mining and energy sectors. Her area of focus is on underground mine ventilation. Her experience includes the design of primary and secondary ventilation systems, traditional chiller refrigeration and direct combustion heating systems, the design of innovative thermal storage systems for heating and cooling, and the design of underground ventilation infrastructure equipment, including ventilation on demand systems.
Comments