A technical look at conveyors
Some consider them eyesores, others think they’re almost pieces of art, but regardless of how people look at them, conveyor systems are a bit of both in that they do create a distinct impression.
Like them or not, there’s no mistaking what these structures are, and what purpose they serve.
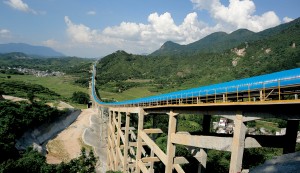
Conveyor in China.
From the back of hay wagons to the top of barn lofts, from basements to wheelbarrows, to the far-reaching depths of massive mines, conveyor systems are the tools of many trades, including mining.
In fact, long before they became common fixtures on many mine sites, primitive conveyor belts have been used since the 19th Century.
In 1892, Thomas Robins began a series of inventions which led to the development of a conveyor belt used for carrying coal, ores and other products. In 1901, Sandvik invented and started the production of steel conveyor belts, and in 1905, Richard Sutcliffe invented the first conveyor belts for use in coal mines which revolutionized the mining industry.
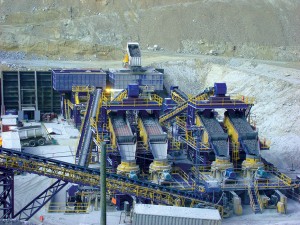
Weir conveyor at a copper mine in Chile.
Today, conveying systems are found throughout the world as they carry huge amounts and weights of materials underground, over mountains, and across vast expanses as they span deep valleys and gorges.
They are almost unstoppable as they conquer seemingly unbeatable obstacles in their quest to deliver massive amounts of materials with reliability and ease.
And, like the materials they carry, they differ in design and strength.
The longest (belt) conveyor system in the world is in Western Saraha. It’s 98-km long and runs from the phosphate mines of Bu Craa the coast south of El-Aaium.
The Boddington Bauxite Mine in Western Australia is officially recognized as having the world’s longest and second-longest single belts with a 31-km-long belt feeding a 20-km long belt. This system feeds bauxite through the difficult terrain of the Darling Ranges to the Worsley Alumina refinery.
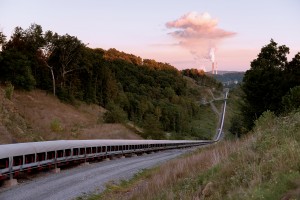
Joy overland conveyor at a coal mine in West Virginia.
The longest single-belt international conveyor runs from Meghalaya in India to a cement factory at Chhatak Bangladesh.
It’s about 17 km long and conveys limestone and shale at 960 tons/hour, from the quarry in India to the cement factory (7-km long in India and 10-km long in Bangladesh).
The conveyor is actuated by three synchronized drive units for a total power of about 1.8 MW supplied by two drives at the head end in Bangladesh, and one drive at the tail end in India.
The conveyor belt was manufactured in 300-m lengths on the Indian side and 500-m lengths on the Bangladesh side. The idlers, or rollers, of the system are unique in that they are designed to accommodate both horizontal and vertical curves along the terrain.
Dedicated vehicles were designed for the maintenance of the conveyor, which is always at a minimum height of 5 metres above the ground to avoid being flooded during monsoon periods.
These are just a few examples of the extraordinary dimensions and capacities of today’s conveyors systems.
It’s long been argued that conveyor systems are cheaper to operate and contribute more to the bottom-line savings than trucks when it comes to moving materials, but like trucks, they do require routine service and maintenance because of their design and component makeup.
As mentioned earlier, conveyor systems are designed to include a number of idlers, rollers, bearings and belts that require servicing because of the harsh treatment they experience from the constant pounding they receive from the heavy payloads they carry.
Naturally, belts are subject to the most wear and tear but seemingly indestructible metal frames and other undercarriage components also require routine inspection to help ensure that the entire conveying system is rigid and balanced.
Regardless of their seemingly bullet-proof designs, conveyor systems are like all other pieces of equipment on a mine site in that they require routine service and maintenance, and unless owners and operators follow the manufacturers’ guidelines, production can stop without warning because of an equipment failure.
And, as everybody knows, mining cannot afford breakdowns.
Comments