A Giant’s Legacy
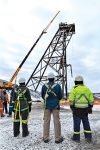
Dismantling the C-shaft in 2015.
CREDIT: CROWN-INDIGENOUS RELATIONS AND NORTHERN AFFAIRS CANADA
The Giant mine, located just 5 km from the city centre of Yellowknife in the Northwest Territories, produced more than 7 million oz. of gold over its entire history, starting in the 1940s. Through the ore roasting process, the mine also produced an enormous amount of highly toxic arsenic trioxide dust. When the owner of the mine went bankrupt in 1999, the cleanup of the site fell to the federal government.
If the project gets its water licence approved, full remediation could finally get under way in 2021 and be completed in 2030. CMJ spoke to Natalie Plato, deputy director for the Giant Mine Remediation Project in May about the site’s history and progress towards its remediation.
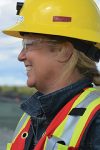
Natalie Plato
Canadian Mining Journal: Tell us a little bit about the history of the Giant mine site.
Natalie Plato: The mine began production in the ’40s and operated to 1999 and was one of the largest gold mines in Canada. But in 1999, the owner at the time, Royal Oak Mines, declared bankruptcy and walked away from the site at which time the federal government under DIAND (Department of Indian Affairs and Northern Development) took responsibility for the site. We had an interim operator, Miramar, and they operated the site for us until 2004. When they finished, they left the site and it officially became abandoned.
At that time, DIAND, or CIRNAC (Crown-Indigenous Relations and Northern Affairs Canada) as we’re called now, developed a remediation plan and took responsibility for the remediation of the site. In 2007, we submitted our Closure and Reclamation Plan to the Mackenzie Valley Land and Water Board, outlining how we were going to remediate the site.
During that water licencing process, we got referred to environmental assessment by the City of Yellowknife, citing significant public concern. We were in an environmental assessment until 2014, at which point we came out of the EA with 26 measures and a number of suggestions that needed to be met before we could go back into the water licencing process. Since 2014, we’ve been working on meeting those measures and now we have resubmitted a post-environmental assessment information package to the Mackenzie Valley Land and Water Board, and re-initiated the water licencing process as of April 1.
CMJ: Can you give us a little more context about the necessary remediation? How polluted is the site from more than five decades of gold production?
NP: During the operation of the mine, one of the by-products of the mining process was arsenic trioxide.
During the early days of the mine, the dust went up the stack and was left to settle where it may. Once they realized that this wasn’t an acceptable practice, they captured the dust and they piped it underground into old mining stopes or even purpose-built chambers. There’s 237,000 tonnes of arsenic trioxide dust stored underground at Giant. That would be the main legacy pollutant, but as I mentioned, some of the dust did go up the stack in the earlier years, so there’s some surface contamination from aerial deposition of the dust as well, along with what would be more traditional tailings ponds – there’s four tailings ponds at site. And there are approximately 100 buildings and structures onsite as well.
CMJ: Some rehabilitation has already taken place at the site. What has already been done and what is left to do?
NP: We need a water licence to do the remediation so in the meantime, the site has been in care and maintenance and continuing to deteriorate. We have already addressed measures that were deemed high-risk and emergency measures.
One of the biggest ones was the roaster complex, the building where the actual arsenic trioxide dust was produced. It was deteriorating very rapidly so we dismantled it. Obviously, that was a very contaminated building so it was done very carefully, under negative air pressure, fully wrapped from 2012-14.
The waste is currently still stored at Giant until we can put it underground with the rest of the arsenic trioxide. That would be the main one that was done. A couple of the shafts, like the C-shaft head frame, the iconic structures of Giant, have been taken down as well.
CMJ: Regarding the main remediation plan that you need the water licence to actually start on, where is the permitting process right now and how far away are you from actually starting work?
NP: We submitted all the paperwork on April 1 of this year, so we have the preliminary schedule from the Mackenzie Valley Land Review Board, and if the schedule doesn’t change, closing statements will happen in March 2020 and we anticipate we would have a licence sometime in the summer of 2020 and then we would start work in 2021.
CMJ: What are you doing currently at the site?
NP: Care and maintenance is the No. 1 item that we’re continuing to do. We are continually pumping and treating water to keep the site safe and keep the surrounding community safe. Right now we’re in the water licencing process so we’re doing some studies to advance the designs, for instance on the tailings, we’re designing our cover right now. We have some studies looking at what the tailings are made of and drilling in the tailings, but other than that, the work would be quite minimal.
CMJ: The water that you need to pump and treat, is this from the underground workings?
NP: Yes, because we keep the water pump below the arsenic chambers, currently we are continually pumping water from the underground mine. We store it and we seasonally treat it and discharge it. If we didn’t do this, the mine would flood and the arsenic chambers would get water in them and there could be a potential release of arsenic trioxide.
CMJ: Planning for the remediation project started a long time ago – the plan was finalized in 2007, but how much has the plan changed since then?
NP: When we resubmitted on April 1, we had to outline what some of those changes were. I can highlight a couple. One of the ones we heard from stakeholders was regarding the eight open pits onsite. Originally, we had planned to leave them open, but we are now planning to fill them with solid material. Another big change was the tailings cover. We had originally proposed a vegetative cover, but hearing from stakeholders, there was a desire for a rock cover. All of the tailings ponds will have engineered rock covers.
CMJ: As you mentioned, the biggest part of the rehabilitation project will be safely securing the 237,000 tonnes of arsenic trioxide dust underground.
Can you describe the method that will be used and why it was chosen?
NP: Sure. The methods to contain the arsenic trioxide were studied quite extensively – we looked at over 50 different options and the one that was chosen is called the freeze, or the frozen block. It’s basically creating a frozen shell around all the chambers to keep water out and keep the dust contained. We looked at a number of ways to do that and the method we settled on is using a passive technology using thermosiphons. Thermosiphons are a common technique to keep ground frozen in the north. It uses a tube charged with carbon dioxide that basically extracts heat from the ground using air temperature so it doesn’t require power and keeps ground frozen. It’s commonly used to freeze building foundations. So we’re going to use that to surround the rock around the chambers of arsenic trioxide dust to create a frozen block and contain the arsenic trioxide.
CMJ: Is this a permanent solution?
NP: Our project was given licence for 100 years and this is not considered a permanent solution, but it’s the best solution we have right now. In the meantime, we are funding the Giant Mine Oversight Board to do research into a permanent solution.
CMJ: Is there any concern about using this solution given the warming climate in the Arctic?
NP: Certainly because it is using temperature, it’s something we have to fully incorporate into our design. We do use the latest climate change predictions as well as obviously having contingency and room for changes, so it’s something we’re continually looking at and modelling. We will also be monitoring the freeze at all times and we will have a presence on the site, so it’s something we can adapt to as well. We’re looking at ways we might be able to incorporate active freeze as contingency should it be needed. We’re certainly looking at all the climate change models and taking it into account in that design.
CMJ: Parsons was awarded the lead contractor role for the project in 2018 – Can you outline what their responsibilities are vs. the Giant Mine Remediation Project team’s responsibilities?
NP: Parsons is the main construction manager. They’re not performing any of the work, they’ll basically be contracting the work for us. They’ll be advising us on how to package the work from a constructability lens as well as timing, help us manage all those contracts and make sure they’re appropriate to the work force.
ARSENIC TRIOXIDE
To liberate the gold found in the arsenopyrite ore at the Giant mine, the ore had to be roasted at extremely high temperatures, which produced toxic arsenic-rich gas. Early on, much of that arsenic was released directly into the environment.
In 1951 a Cold Cottrell Electrostatic Precipitator, which acted as a scrubber, was installed, removing a lot of the arsenic trioxide waste. As a result of adding a second scrubber – a Hot Cottrell Electrostatic Precipitator – to the roasting process in 1955, arsenic releases were further reduced from 7,400 kg per day in 1951 to 2,900 kg in 1956.
In 1958, a Dracco baghouse was added to collect the waste, reducing airborne arsenic emissions to 52 kg per day by 1959.
Over the years, that number would fluctuate up to 300 kg per day. Since the waste was collected instead of released, it needed to be safely stored. In the 1950s, scientists and government agencies agreed storing it in underground stopes and chambers was an appropriate, long-term solution. They believed that, when Giant mine closed permanently, the natural permafrost in the area would re-establish around the storage vaults and seal in the arsenic trioxide.
– Adapted from www.giant.gc.ca.
WATER TREATMENT
The existing effluent treatment plant at Giant only operates seasonally, during the summer. Mine water pumped out of the underground mine goes to the Northwest Pond to be stored before treatment. Any surface water than needs to be treated is also pumped there and then to the plant for treatment; treated water is released to Baker Creek.
The remediation plan includes the construction of a new and water treatment plant that would operate year round, remove more arsenic from the water, and release treated water into Yellowknife Bay.
Comments