Intelligence in mining: Automation’s next frontier
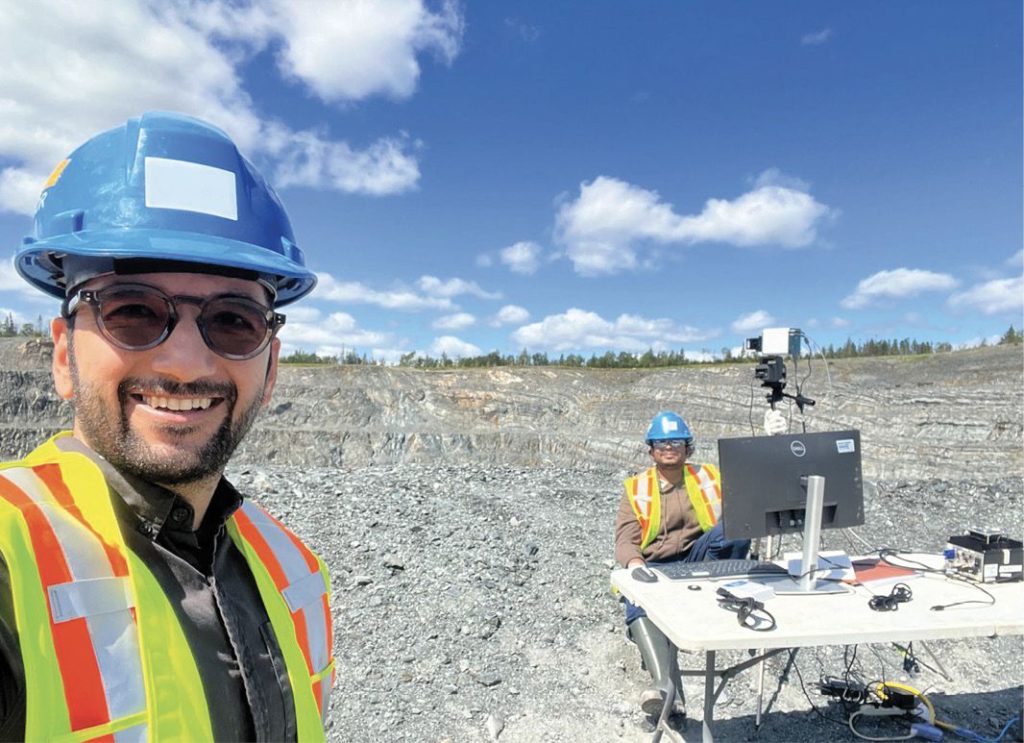
The theme of this year’s MINExpo was unmistakable: Automations that are reshaping the industry. From Caterpillar’s fully autonomous loaders to robotic companies eliminating on-site safety concerns, the scale of these intelligent solutions signals a transformation toward intelligence-based automation.
Automation in mining has been centered on engineering for decades — conveyor belts, robotic arms, and self-operating machinery that boosted productivity by reducing manual labour and human error. These mechanical systems enhanced efficiency bound by constraints of operation upstream. Data management automation redefined how companies handle vast information troves. Cloud solutions offer scalability and flexibility, enabling real-time operational oversight. Yet, in the chaotic and heterogeneous realm of chasing ore deposits where data volumes have surged exponentially, geologists still bear the burden of interpretation because of the sub surface’s inherent complexity.
A leap beyond mere mechanization or data processing is intelligence-based automation! This form of automation does not just execute commands; it comes to adapt, learn, and anticipate to better constrain geological variables and support operational decision making. Intelligence on variability of ore zone on daily basis provides critical insights to optimize ore extraction, grade control, and real-time adjustments. In an industry where incremental improvements can translate into millions saved, such intelligence offers a significant return. Whether optimizing blasting grid placement or predicting supply chain disruptions, intelligence-based automation unleashes downstream mechanical and data automation.
A close look at the key stages of the mining process helps better grasp the scale of this disruption. The mining process is comprised of drilling and blasting; loading and hauling; crushing and grinding; concentration; and smelting or refining. Efficiency gains early in this chain create a snowball effect, amplifying benefits downstream. Poor separation of ore from waste at the mine face marginalizes overall performance. Suboptimal positioning of blast hole grid can ripple through operations — more accurate separation means loaders handle less waste, boosting their efficiency. Consequently, the milling process benefits from higher ore grades, improving throughput and reducing energy consumption.
Realtime refinement of block model debottlenecks downstream production efficiency and delivers substantial cost saving across the operation. Relying on coarse models intended for resource estimation during production can be disservice to engineering investment downstream where we count minutes and seconds to calculate gained efficiency. This practice should have been long gone!
However, hurdles remain in mining to adapt new technologies, and the absence of one-size-fits-all solutions impedes widespread adoption of intelligent systems. The behavioural cost of adapting to granular-scale intelligence is significant. A data-driven culture can actionable insights into daily operations — a shift that requires embracing agile methodologies and continuous improvement; areas where the industry has traditionally lagged.
Implementing intelligent blasthole positioning and advanced ore-waste separation technologies also demands real-time, purpose-fit intelligence before the shovel hits the ground. In the high-stakes environment of mineral extraction, delays or data inaccuracies can cascade into costly inefficiencies. The solution must process geological data instantaneously and adapt to each site’s unique conditions — a challenge that off-the-shelf solutions rarely meet. It also calls for engineers who think like geologists and vice versa!
Scient is stepping into this gap, providing hardware and software infrastructure for real-time ore body knowledge at mine sites. Scient has deployed its technology on diamond drill core samples at the tale of exploration, the face of open pit mines, and on chips coming out of blast holes before engaging shovel. This sweep of analysis at micro and macro scale offers unparalleled control over mining and excavation process — something the status quo still inherently lacks. The technology refines geological models through identifying alteration patterns and minerals invisible to the geologist’s eye. Scient’s technology application in the production stage — where the environment is better constrained — enhances the understanding of mineralization for precision mining.
The winners of automation challenge are those who prioritize automation of ore body intelligence to avoid marginalizing mechanical and cloud-based automation. In mining, where stakes are high and margins thin, such integration promises not just cost savings but smarter, more responsive operations.
Masoud Aali is the CEO and founder of Scient. He holds a PhD in exploration geophysics and has over a decade of experience across various natural resource exploration sectors. Prior to founding Scient, Masoud held a postdoctoral entrepreneur fellowship at Polytechnique Montreal through IVADO (Institut de valorisation des données), where he led initiatives to bring cutting-edge signal processing and machine learning research into commercial applications for characterizing subsurface properties.
Comments