Driving peak performance in modern mining with high-torque, low voltage motors
How high torque electric motors are designed to endure the rigors of harsh mining environments while bringing new levels of sustainability to the mining industry
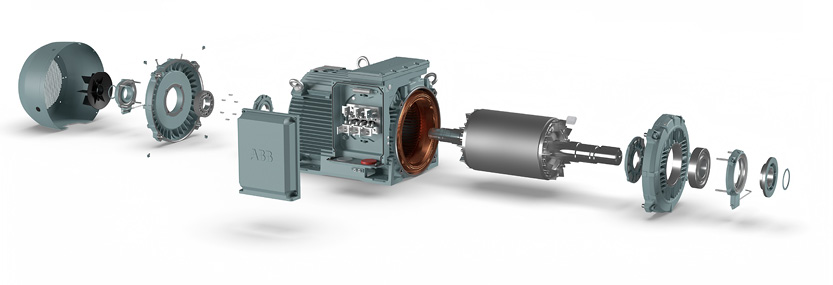
In the pursuit of efficiency and productivity, modern mining hinges on equipment reliability across all stages — from exploration to processing and transport. High torque motors are pivotal in this ecosystem, powering essential machinery like crushers, mills, and conveyors. Their role is indispensable in ensuring operational continuity and economic success.
Mining environments pose unique challenges for electric motors, exposing them to dust, moisture, vibration, and extreme temperatures. Dust leads to component wear and overheating, while moisture can cause electrical shorts and corrosion. Vibration induces misalignment and bearing damage, risking motor failure and operational downtime, which negatively impacts schedules, budgets, and above all, profitability.
Designers of motors for mining machinery must also account for various use conditions, including improper speed control by operators as well as the slow operation needed during routine belt inspections. Instances of overspeeding and sudden stops cause significant wear and mechanical strain. Ensuring smooth, robust, and simple operation is key to mitigating these risks and enhancing motor reliability.
Selecting the appropriate motor for a specific mining application is a crucial decision. Factors like motor size, power rating, efficiency, and operating environment must be meticulously considered. Oversizing a motor can lead to inefficiency and unnecessary energy consumption. Undersizing a motor can result in overloading, overheating, and premature motor failure. Hitting the “sweet spot” of motor sizing often requires motor manufacturers to find creative ways to increase power density in smaller spaces.
Powering productivity
In the demanding world of industrial mining and bulk material handling, severe-duty and process performance motors are the unsung heroes. Paired with variable frequency drives (VFDs), these motors provide the high torque that is essential for belts or conveyors in the high-vibration, dusty, and dirty environments typical of outdoor settings.
Precise motor sizing is critical for performance, ensuring they can withstand stress from emergency stops and resist severe impacts of shock loading — whether from rock dumping or temperature-induced jamming. Durable windings in these motors combat vibration and supply necessary torque to prevent costly downtime.
Operators often push these motors to their limits, leading to potential overspeeding or overloading, which necessitates extremely robust construction. Load-sharing capabilities (within the VFDs) between lead and follower motors can help maintain operational harmony and protect the costliest component of conveyor systems: the conveyor belts.
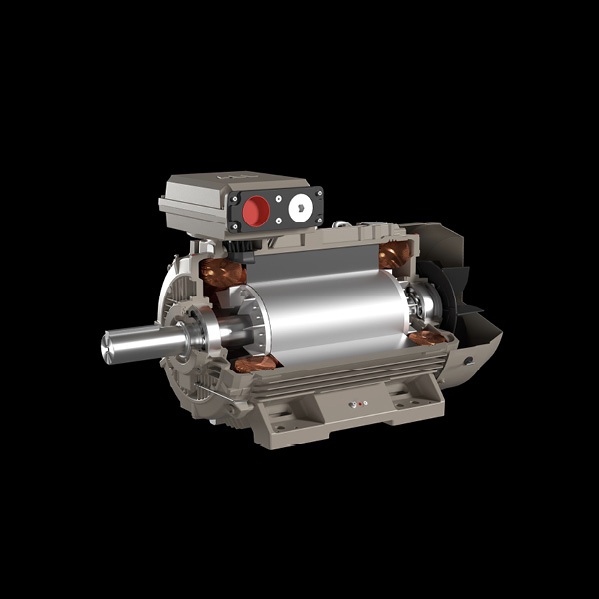
For maintenance, motors must operate at ultra-low speeds, or “creep”, to facilitate periodic belt inspections. This need for resilience, precision, and adaptability make high-torque severe-duty motors indispensable for continuous operations in challenging environments.
Variable frequency drives (VFDs)
Mining operations demand reliable, 24/7 equipment, making durability and extended life critical. Although VFDs have become popular in low voltage applications, it is estimated that only 10% to 15% of large motors use VFDs because of the high costs and complexity. VFDs enable soft starts for large motors, reducing thermal stress and insulation damage, thus extending motor life.
Unlike traditional mechanical drive systems with multiple components like variable-speed fluid couplings, VFD-based motor-drive systems have fewer moving parts, resulting in less need for maintenance and fewer potential failure points. They also offer precise speed and torque control, adapting efficiently to varying loads, and with proper maintenance, often outlast traditional systems.
Motor selection matters
Choosing a reliable motor manufacturer with a strong track record offers significant advantages. Established manufacturers possess the expertise to design motors that can withstand the rigors of mining environments. Their understanding of the specific challenges faced by mining operations can translate into motors and drives with features like the following:
Robust design: Utilization of high-quality materials and robust construction techniques ensures durability and extended operational life. Features like sealed bearings, enhanced cooling, high ingress protection, low vibration, and corrosion-resistant components contribute to a motor’s ability to withstand harsh environments.
Tailored solutions: Mining applications are diverse, with varying needs for motor size, power rating, and specific operating conditions. Reputable manufacturers often offer both standard configurations and customized options, ensuring a perfect fit for each application.
Expert support: A reliable motor manufacturer provides comprehensive global support beyond the initial purchase. This can include readily available spare parts, on-site service expertise, and technical support to address any operational challenges.
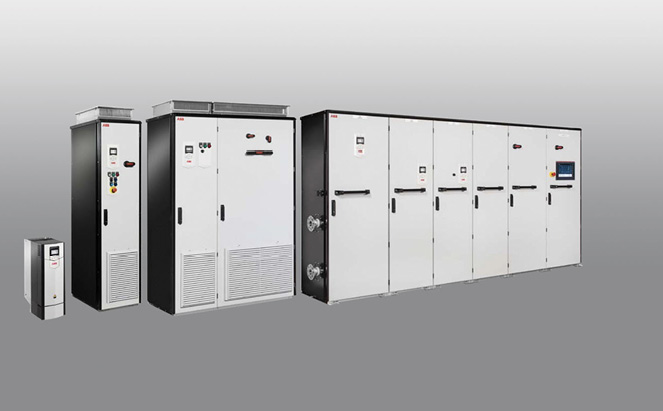
End-to-end solution: Choosing a partner that has expertise in providing a solution from concept to commission ensures that the entire system is optimized for efficiency and reliability in mining operations.
Wide portfolio: A single manufacturer’s ability to provide solutions across the spectrum of motor and drive needs can simplify sourcing and future service requirements.
Long-term thinking
Reliability offers long-term benefits beyond just technical specifications. Minimized downtime is a critical factor for maximizing productivity throughout a motor’s lifecycle. Rugged motors designed for harsh environments, coupled with preventative maintenance practices, can significantly reduce downtime associated with motor failures. Predictive maintenance programs, utilizing vibration analysis, and temperature monitoring, among other analytics, can further minimize the risk of unexpected failures, allowing for proactive maintenance scheduling.
High-efficiency motors contribute to mining operations by consuming less energy to deliver the same output. This translates to lower energy costs and a reduced environmental footprint. Modern motors often incorporate features like optimized stator and rotor designs and advanced bearings to minimize friction losses, leading to improved efficiency.
While the upfront cost of a high-quality, well-suited motor may be slightly higher than a standard motor, the long-term benefits outweigh the initial investment. Reduced downtime, improved efficiency, and lower maintenance costs contribute to a lower total cost of ownership over the lifespan of the motor. Investing in reliable motors can yield significant financial returns over the course of a mine’s operation.
Real-life applications
The Mining Association of Canada reports that Canada’s mineral exports increased to $153 billion in 2022, making up 21% of Canada’s total merchandise exports. The bulk of Canada’s exports, 57% in 2022, were to the United States. The United Kingdom (9.2% in 2022) and the European Union (7.8%) were also significant export destinations. The mining industry in Canada is not just increasing in size, it is also becoming increasingly global.
This is because mining, as an industry, has always sought to push the boundaries of what is possible. After a slump in the last decade, the industry is returning to prevalence, and long-standing suppliers like ABB are finding a landscape that is both familiar and transformed. Previously dominant in medium voltage (MV) dual-drive systems, ABB has now expanded its focus to low-voltage, high-torque, high-horsepower overland conveyors, highlighted by projects like Inverta in Chile.
Historically, ABB tackled the challenges of hard rock mining, which demands robust machinery. Advancements in conveying mined materials from underground to above-ground hoppers have been substantial, with motors ranging from 400 to 600 hp featuring NEMA D flange designs and zero-alignment gearboxes. These innovations have introduced a new era of reliability and efficiency, with machines capable of running for up to 20 years when properly maintained.
Today, the challenge is efficient material conveyance. From 300-hp motors to the widespread use of IE4-rated, severe-duty motors, mining continues to scale up. The industry has shifted towards high-horsepower low voltage solutions — a significant change from the days when anything over 300 hp required 4 kV. Now, 460 V systems can handle over 1,000 hp, even in diverse electrical environments like those in South America.
As global mining rebounds, driven by the rising demand for lithium and other essential minerals for modern technology like EV batteries, manufacturers are poised to meet these evolving needs. Mining equipment manufacturers have undergone a rush of mergers and acquisitions exemplifying the consolidation trend in an industry always in motion. While coal may be fading, mining’s inherent momentum remains strong, underscoring a dynamic and ever-adapting sector.
Improved operational efficiency
The reliable and efficient operation of motors is crucial for mining success. By selecting high torque motors designed for harsh conditions, prioritizing energy efficiency, and partnering with trusted manufacturers, mining companies, regardless of size, can reduce downtime and costs.
With pressing environmental concerns front of mind, it has been, and continues to be, vital for the motor industry to proactively research, develop, and adopt low-carbon technologies to push beyond basic compliance and lead the way toward greater sustainability. It is now up to the ambitious leaders in the mining industry to select those partners whose products and practices embody that vision.
As mining embraces a future-focused approach, featured prominently across all three of the show floors at the recent MINExpo2024, electric motor and drive use will evolve to prioritize sustainability through lifecycle assessments while simultaneously leveraging smart technologies like predictive maintenance, to optimize performance, minimize environmental impact, and ultimately drive long-term productivity gains.
Robert Boyce is the U.S. division manager for IEC low voltage motors at ABB. For more information, visit new.abb.com/motors-generators/iec-low-voltage-motors.
Comments