Embracing automation for feeder control
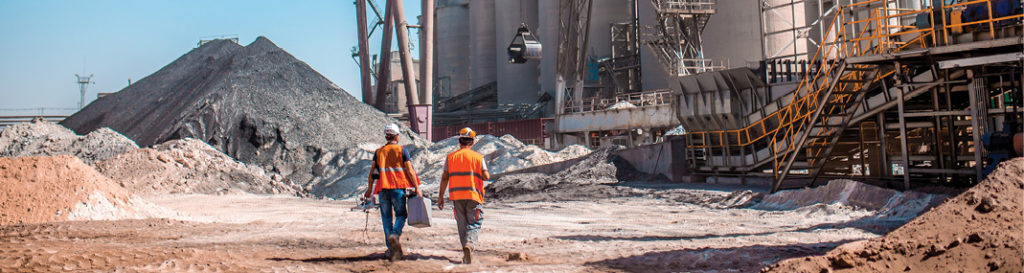
The ancient Egyptians built monumental structures like the Great Pyramids, where huge limestone and granite blocks were carved by hand after being extracted from local quarries. Today, as the demand for construction materials persists, mining remains indispensable but transformed by technological advancements. With a focus on automation, modern mining operations are seeing a surge in efficiency and safety measures.
The feeding process, whether for screening, crushing, or washing, is critical for overall efficiency. Typically, a feeder, acting as a reservoir, steadily dispenses materials into the processing plant at a controlled rate. The synchronization of this rate with the processing machinery’s capabilities is essential for maintaining productivity.
According to the government of Canada, in 2022, Canada produced over 60 types of minerals and metals worth $75 billion. Based on these figures, it is no surprise that Canada is a leading global producer of several critical minerals essential for clean energy technologies. This has fuelled continued industry growth.
Take, for instance, Canada Nickel, a Canadian company engaged in advancing its nickel-sulfide projects to deliver nickel required to feed the electric vehicle and stainless-steel markets. In 2027, it aims to begin production in Ontario and process 80,000 t/y of nickel. For production of this scale to be successful, even small productivity gains can have a significant impact on a mine’s bottom line.
However, it is not just in Canada where mining operations are expanding. Demand for mined materials is global. In fact, the Mineral Products Association (MPA), the trade association for the aggregates, asphalt, cement, concrete, dimension stone, lime, mortar, and industrial sand industries stated that, in a typical year, the U.K. alone uses 250 million tonnes of aggregates. To meet this demand, optimization of processes, like feed control is key.
Challenges of manual feeder control
Traditional manual feeder control methods involve operators using earthmoving equipment to regulate material flow into the hopper. However, this approach presents several shortcomings. Manual adjustments often result in inconsistent feeding rates, leading to inefficiencies and reduced productivity. Moreover, human error can lead to overloading and equipment damage, increasing operational challenges.
To avoid these problems, the operator must regulate the feeding speed based on the processing capacity of the plant. However, relying on a manual process often leads to variations in feeding rates.
Advantages of automation
Automating feeder control avoids these issues and allows for precise adjustments in material flow rates. By factoring in geological conditions, such as hardness and fragmentation, engineers can fine-tune extraction and processing processes with unparalleled precision, based on their in-depth knowledge of the mine’s geography.
For example, when dealing with particularly hard or abrasive materials, feeder rates can be adjusted to minimize wear and tear on downstream equipment, thereby improving the overall productivity and curbing maintenance cost caused by equipment damage.
While automation promises efficiency, its implementation must also prioritize workforce considerations. By automating tasks traditionally performed by personnel, mine operators can reduce the risk of worker accidents or injuries. This, in turn, allows for the reallocation of human resources to more strategic roles like data analysis, process optimization, or equipment maintenance.
Beyond reducing worker accidents, automation contributes to an overall safer working environment through the implementation of advanced safety features. This could include collision avoidance systems, like using sensors and real-time data to detect potential collisions between vehicles or equipment, prompting automatic interventions to prevent accidents. Furthermore, automated emergency shutdown procedures are also a crucial safety mechanism in mining operations. This should include procedures for swift response to emergency situations and ensuring the protection of personnel and assets.
Dispelling misconceptions of automation
A common misconception surrounding automated feeder control is the notion that higher speeds equal increased throughput. Contrary to this belief, optimal feeder control maintains a steady pace. Meaning that a controlled feeder can result in higher throughput by maintaining a more constant pace — as opposed to forcing rapid feeding.
If you feed at the correct speed for the equipment, then you get elevated levels of efficiency, and the product will be of higher quality. This method also reduces stop-start cycles and improves overall efficiency, providing an energy saving opportunity by minimizing wasteful operations.
Remote monitoring and control
Deployment of automated monitoring and predictive maintenance systems can also help minimize downtime in automated feeding. Using such systems offers mine operators real-time access to critical operational data, allowing them to oversee equipment performance, material flow rates, and environmental conditions from anywhere.
This facilitates proactive decision making by providing insights into production trends and potential equipment issues. Systems can detect potential issues before they escalate, reducing the likelihood of equipment breakdown and downtime.
Solutions for industry
Technidrive has developed a solution for automated feed control using technology, including WEG’s CFW11 variable speed drive (VSD) and Vega 80GHz radar sensors. The system operates on a proportional-integral-derivative (PID) loop feedback control system. A PID controller adjusts the control variable, such as motor speed, in a feedback loop to minimize the difference between the desired setpoint and the actual value of the process variable. This achieves precise and stable control of the system.
Using VSD control, this system regulates material flow rates by adjusting motor speed as required. Radar sensors detect specific material levels in the plant, while data on electric current drawn by crushers during operation is collected to create a PID loop. This loop continuously analyzes feedback from sensors to automatically adjust feeder speeds, maintaining optimal material flow rates and preventing overfilling.
Maintaining the optimal level of material in the crusher is essential, as overfilling can lead to inefficiencies, increased power usage, and reduced throughput.
The radar sensors effectively grant the plant its own decision-making capabilities regarding material requirements for efficient operation. If material levels decrease, the system automatically speeds up the feeder and vice versa.
While the fundamental task of extracting materials from the earth remains unchanged, advancements in technology has propelled us forward, presenting innovative solutions to enhance efficiency and safety. By embracing automation, such as innovative feeder control systems, mines can streamline operations, reduce downtime, and focus on worker well-being.
David Strain is technical director at integrated automation system expert, Technidrive.
Comments