Automation provides solutions for sustainable mining
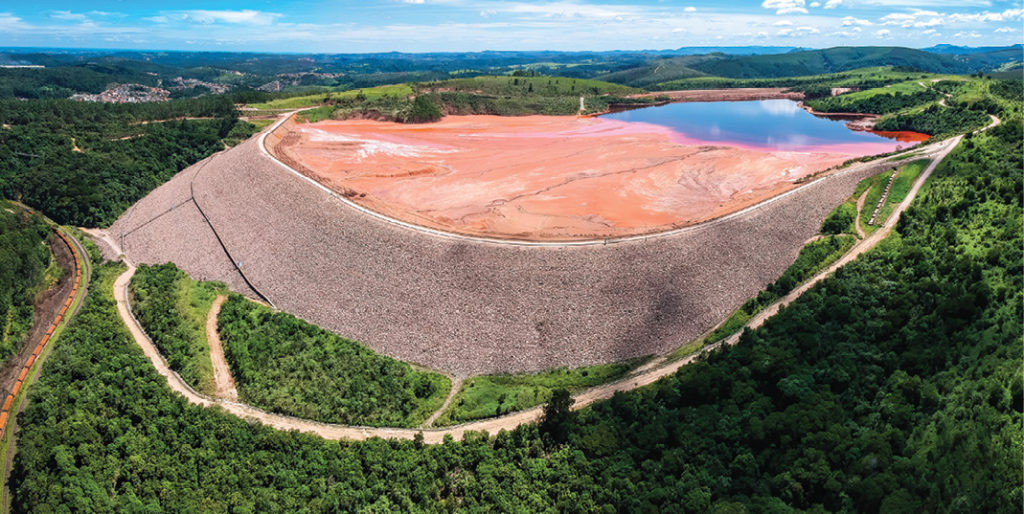
A prevailing challenge for the mining industry, which has taken on even more prominence recently due to a greater focus on the environment and sustainability, is waste and waste management. From the conservation of lakes and rivers that are being polluted to the sequestering of tailings ponds at mining sites, managing waste to mitigate the risk of damage to natural resources demands investment and concerted efforts into water treatment programs. While the benefits of such investments and efforts are apparent to most, this also creates a novel set of problems. As such, companies will need to turn towards the latest technologies to access energy and ensure all regulatory mandates are being met. All this while not only trying to reduce their environmental footprint, but also raising the capital necessary for putting forth such vigorous programs – not an easy task for a cost conservative industry like mining.
This is where automation and robotics solutions come into play to help the industry. Once the decision is made to bring automation to site, whether it be a standardized product or a custom-tailored solution for various applications, the improvement may not be obvious at first, but the return on investment will be tenfold in the span of mere months. To make a positive and sustainable impact on the economic role in society, mined materials, which are explored for, extracted, transported, and processed according to quality control processes, have to be delivered safely, whilst retaining high quality.
As an example, let us consider tailings which have long been considered waste. Advancements in technology and the need to meet the demands of a circular economy are now shifting this traditional perspective. The long-standing approach has been to pump tailings into artificial settling ponds where solids and liquids could be separated. As the design of thickeners has improved, so has the dewatering process wherein water treatment and recovery are more efficient and effective. Measuring the zeta potential of these systems allows for the optimal amount of coagulant to be added to thickeners to maximize the formation of flocs and subsequently separation of solids and liquid components that can then be directed to proper channels for storage, re-use, or return to the environment (as per regulatory practices). Fast phase identification and quantification to quickly respond to changes in the processed products to ensure optimal quality and reduce wastage is a necessity in this case. Moreover, identifying compounds of value that can be recovered from tailings and thus reduce wastage and potential environmental damage is of utmost importance. Evaluating groundwater movement and pollution by quantifying pore size is a solid approach to avoiding contaminants.
In keeping up with the subject of high-quality production and embracing automation, when looking at time saving measures, a fully automated environment allows for 24/7 operation minimizing downtime and maximizing productivity. Another cost saving approach to avoiding downtime while implementing automation would be to measure the density of both dry solids and formulations for accurate fine-tuning of density from individual values and blends of cuttings, barite, clays, and other solids to minimize cost and prevent blow-out. Automated measurements allow personnel to focus on more pressing, high-value tasks while mundane, routine work is expedited. This can be utilized in either a laboratory environment, or as much as a production site. While personnel can be onsite, automation in the laboratory can ensure proper viscosity of bentonite at rest and during pumping. This allows for smooth processing when drilling mud is transported as well as no sudden downtime.
Taking a more focused approach to cleaning as an example, rather than dedicating time and human resources to such a time-consuming task, immediate cleaning after a measurement procedure can be robotized to fully automate the process end to end. Even in the case of hard to clean samples, an integrated cleaning unit can be equipped with a cleaning detergent pump to ensure an effective cleaning process, taking the guess work out of it.
Although human error is always a possibility in any process, easy automated processes reduce any potential errors with intuitive and easy-to-handle operating procedures. Automation allows for such sophistication as data integrity insurance, with a unique data matrix code labeled on the bottom of sample cups and allows for integrated code readers. Since measurement results can be directly transferred to network storage, time is saved, process controls with reliable data have been proven, errors due to manual input are avoided, and data integrity preserved. An increase in sample processing capability also increases walkaway time. A built-in pH station for titration and sample preparation before analysis increases storage capacity on average from 36 to 54 samples, providing increased walkaway time and higher throughput.
Sustainable mining of natural resources is a cornerstone of our standard of living and prosperity. Exploring new exploitable deposits and recycling raw materials have to be done responsibly for mining to have that sustainable longevity. A proper investment in automation and robotics will contribute to the development of such programs into the production chain for a healthier environment and to help optimize the exploration process for companies in the coming years.
Atri Maharaj is national sales manager and Garine Sarkissian is marketing manager with Anton Paar Canada.
Comments