The cost of salt
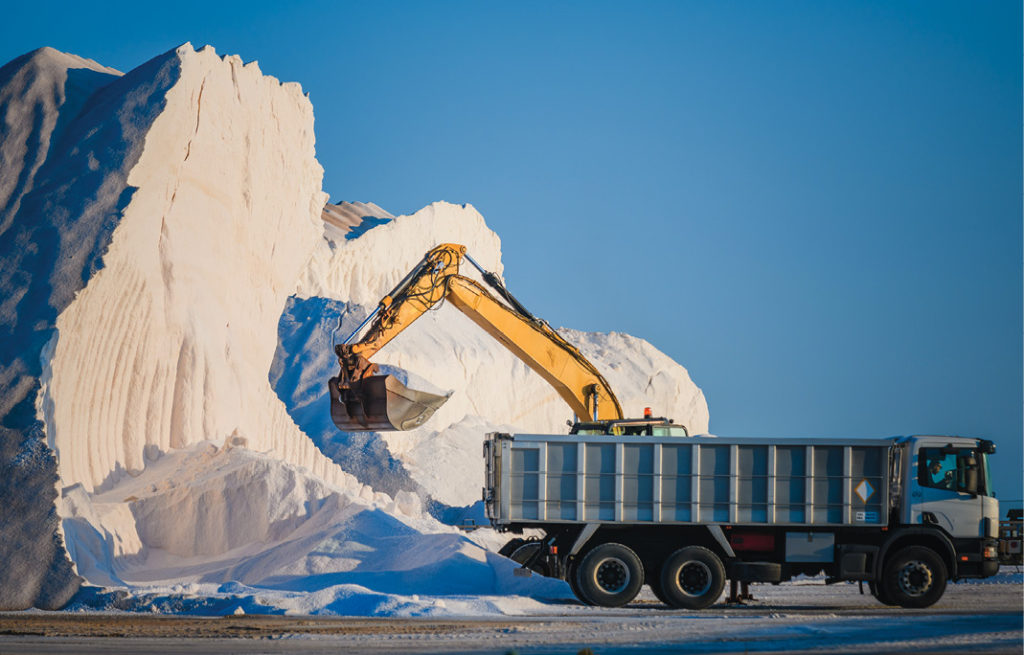
Salt (NaCl), a nutrient vital to all animal life, is an important natural resource especially in southwestern Ontario. Canada is one of the world’s largest salt consumers thanks to its harsh winters, and Ontario provides substantially more of this salt than all other provinces combined. Most Canadian salt is commonly mined via underground room-and-pillar methods and is used to de-ice roadways. Table salt, chemical raw materials, and other end uses also represent major portions of overall consumption. The later products are most often produced via solution mining, where fresh water is injected via wells into buried salt deposits to recover a salt-saturated brine. Solution mining also yields valuable underground caverns, often used to store hydrocarbons after salt production ends.
As mineral resources, the development of salt deposits into new mines generally entails an iterative evaluation process like that of any other mineral deposit, beginning with discovery and scoping-level economic analysis. However, salt deposits are more widespread than most and relatively cheap to extract, a defining characteristic that salt shares with other ubiquitous minerals of economic interest. As with mining other common minerals, transportation costs often form a substantially larger portion of overall operating costs when compared to mineral commodities of higher value. But the mining costs associated with producing salt via room-and-pillar methods can often form a major portion of the overall operating cost, too. And the cost to process salt-saturated brines into table salt can be quite high. Not giving due consideration to these costs during the economic analysis of salt development projects brings with it the potential for poor decision making. To make more relevant investment and development decisions, salt mining and processing costs should be estimated realistically and included in all economic analyses from the first evaluation onward.
To demonstrate the relative magnitudes of these salt mining and processing costs relative to transportation costs, Costmine has modeled the cost of two 2,000-t/d salt mining scenarios. A representative room-and-pillar mine accessed via a 350-metre shaft was modeled alongside a typical single-well solution mine of the same production rate. A 2,000-t/d vacuum pan evaporation plant, to produce table salt from salt-saturated brine, was also modeled to offer a more complete estimate of the cost to produce table salt via solution mining. The overall initial capital cost and average life-of-mine production costs from these models are presented below.
Item | Average operating cost (US$/tonne salt) |
Room-and-pillar mining | $61.44 |
Solution mining | $6.05 |
Processing plant | $211.37 |
Transportation* | $255.00 |
We can see that the transportation cost estimate is clearly our largest operating cost, but the estimated cost to process brine into table salt is also considerable and is within 20% of our transportation cost. While the estimated solution mining operating cost is small from almost any perspective, room-and-pillar mining costs represent about 20% of the overall operating cost in a scenario of mining and shipping rock salt.
The above cost does not include the initial capital expenditure nor the costs of marketing and packaging required before profitable production can be achieved. These costs are considerable and should always be considered before investment or development decisions are made. What has been presented above does demonstrate that, even when shipping costs are relatively high, the costs of production can still be substantial and must be duly considered during project evaluations.
Sam Blakely is a senior mining engineer at Costmine, a division of The Northern Miner Group.
Comments