Opportunities for mining and critical minerals processing in North America
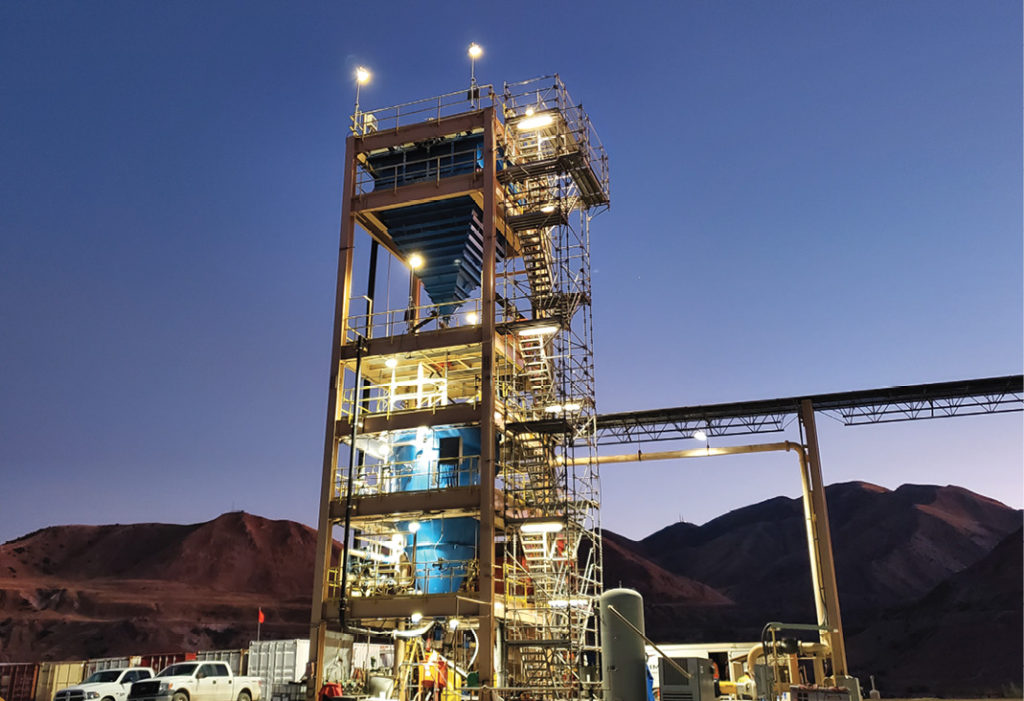
As a response to the previous two decades of expanding globalized trade, governments and businesses in North America are now beginning to pay more interest and concern to the sources of raw materials. This is especially true for strategic metals and minerals that are the necessary building blocks for the net-zero economy. Green materials like nickel, lithium, graphite, cobalt, and copper will be increasingly required for large format rechargeable batteries and infrastructure in quantities that will be hard to achieve and will probably be a bottleneck in the mass acceptance of electric vehicles. It is forecasted that copper demand will increase from about 25 million t/y today to 40 million t/y by 2030 as well as a 44% increase in nickel demand over the same period.
Over the last two decades, China has developed a dominant position in battery manufacturing technology which includes the mining and processing of battery precursor metals throughout the world, in places like the Democratic Republic of Congo for cobalt and Indonesia for nickel. Some of these sources are being newly scrutinized because of a lack of government transparency and regulations, and because some of the sources require much higher uses of energy to process, such as mining and processing nickel laterites compared with nickel sulphides. Ottawa and Washington are both signaling strong action to “on-shore” the mining and processing of green metals in North America. Executive orders from President Biden to support green metal projects in the U.S.A. and the recent federal government announcement for divesting ownership of some Canadian mining companies held by foreign state-owned companies are both part of this trend.
As a result, the mining industry in North America is already seeing a resurgence in activity and investment. This is driven by the drive to electrify energy infrastructure and increase energy self-sufficiency. Along with this, there will be an important driver to extract and process these materials in the most environmentally efficient and sustainable way. This is where companies like Eriez come into the story.
The first step in producing materials after mining is the concentrator, and the basic concentrator flowsheet has not changed much in the last 50 years. Ore at or above the cut-off grade is identified by the mining operation, then it is crushed and ground to a suitable size to enable bulk froth flotation followed by an upgrading cleaner step to produce final concentrate for smelting and/or refining. All this time, the grinding endpoint and consumed energy are driven by the particle size required to float minerals based on conventional flotation. For a typical porphyry copper ore, conventional flotation is not practical for particles above 200 microns, sometimes significantly less, so the endpoint of the grinding operation must be in this range, resulting in excessive grinding and serious challenges for water recovery, since de-watering becomes more difficult as the solids become finer. In a conventional plant, the usual way to address this is to thicken the tails and then pump them to a water impoundment for settlement. In this scenario, a significant amount of the water is lost to evaporation. Water loss means that the water in a concentrator cannot be operated in a closed loop and fresh water is always required. Other de-watering strategies exist, but they are energy and capital intensive.
Eriez has pioneered the commercialization of coarse particle flotation (CPF) with its HydroFloat cell, which is a key disruptive technology that has a major impact on both water and energy, and it will be a key strategy to conserve both. By increasing the size where ores particles can be floated, typically 2-3 times, significantly less grinding energy is required, potentially 30% to 50% less. And because the flotation tail is much coarser, it is easier to de-water and has less retained water.
Eriez introduced their HydroFloat coarse particle flotation equipment about 10 years ago with major base metal producers, such as Rio Tinto, Newcrest, and Anglo American. Early applications focused on recovering “lost” coarse metal units from conventional concentrator tailing streams. This typically represented at least 60% of coarse tails and 2% to 6% global recovery improvement.
Now, the focus is on including the HydroFloat inside the mill circuit as an ore sorter. The first application of this type was successfully demonstrated at Anglo American’s El Soldado during 2021 and is now in full operation. This configuration of CPF allows a significant reduction in grinding energy, conventional flotation capacity, and it produces a coarse tail that can be easily de-watered or combined with conventional tails. As part of their FutureSmartMining family of technologies, Anglo American is piloting a technology to co-mingle coarse and conventional tails in unique ways to produce a waterless dry stacked tail. Eriez is excited about the recent technologies such as low energy water recovery and waterless impoundments that have become commercially possible because of coarse particle flotation.
Another Eriez technology that has been introduced to increase the efficiency of concentrators is the StackCell, a high-rate mechanical cell that uses the two-stage principle. In the first stage, high shear mixing of bubbles and feed slurry occurs to optimize bubble-particle collecting. In the second stage, which is isolated from the first, the bubble-particle aggregates can float by buoyant forces in a fluidic environment with low turbulence and a low energy convective flow that minimizes bubble particle detachment and drop-back. The two-stage flotation technology contrasts with conventional mechanical tank cells where bubble-particle contacting and buoyant separation occur in the same fluidic environment, which cannot be simultaneously optimized for both processes. The StackCell is now operating in commercial flotation applications in several countries. It has been verified that in many scenarios, StackCells can operate with one quarter or less of the residence time required for conventional technology and with 40% less impeller energy. This all means smaller concentrators with less energy use.
Both products are positioned to have a key role in supporting the sustainable expansion in mining of critical and strategic minerals that is underway in North America.
Eric Wasmund is vice-president of global flotation business at Eriez, Asa Weber is global StackCell product manager at Eriez, and Jose Concha is global HydroFloat product manager at Eriez.
Comments