Answering the need for digital transformation
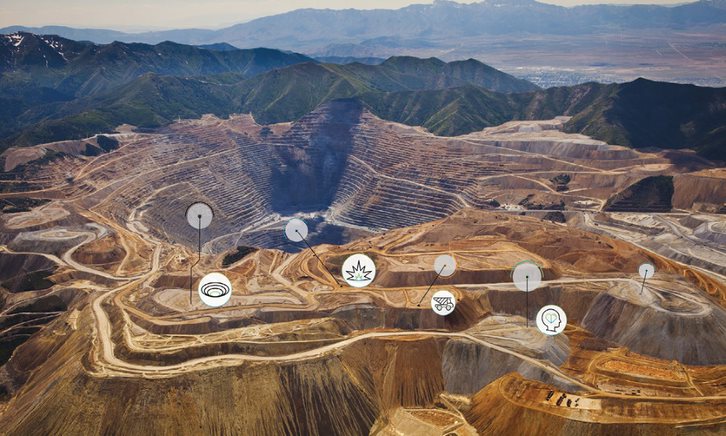
Mines worldwide are under increasing pressure to cut costs and improve productivity, all while becoming safer and more sustainable. These expectations are set against the backdrop of a global pandemic, a highly competitive landscape, volatile fuel and commodity prices, and greater scrutiny by authorities, shareholders and the public.
Digital transformation is widely accepted as the answer to many of these challenges, but digital transformation demands more than niche technology and partial solutions. This is where one technology partner, capable of connecting sensor, software and autonomous technologies, becomes valuable.
Mines empowered with technology to become situationally aware, self-learning and autonomously connected are safer, more productive and can make sense of their data.
The key to empowering this digital transformation is a holistic, life-of-mine approach built on connected sensors, software, infield apps and cloudware. A single onboard ecosystem comprising a smart computer, antenna and display wields the power to connect the mine to the boardroom.
For customers this means a scalable, platform-wide answer to challenges previously addressed by point solutions and multiple vendors: drill and blast, collision avoidance, operator alertness, fleet management, operator assist, machine control, asset health and more. For the industry, it points the way to a safer, more productive and sustainable future.
Incremental digitalization for mining
Incremental digitalization is helping many mines to become more efficient and productive. Most operations are already sitting on mountains of data, which raises the question – are we leveraging this information to its fullest extent?
This question increases in complexity when the data silos and various operational roles are contracted throughout the mine. This, combined with the fact that job roles and responsibilities are changing more quickly than ever, makes it hard to assess.
In this context, partnering with a life-of-mine technology provider can help. Focusing on an autonomous connected ecosystem can support all mining companies, regardless of their operational maturity, allowing them to take small steps.
An integrated safety portfolio, connecting systems for collision avoidance, operator alertness, vehicle intervention and personnel protection, is a good example of this. First, an operator alertness system can combat fatigue and fatigue-related events.
Second, incidences can be reduced with a proven collision avoidance system. This can be upgraded to automated vehicle intervention, taking over the vehicle’s propulsion system in defined situations when the driver does not react to an alert.
Ultimately, mines can introduce a fully autonomous solution, removing the human element altogether through self-driving vehicles. The precursor to autonomy involves identifying and processing the right data at the right time to make the right decision with the proper feedback, and this is where many mines are now.
For example, an autonomous mission management system launched by Hexagon and Liebherr, orchestrates autonomous fleet and unmanned mine traffic movements throughout the mine for optimized autonomous haulage.
The autonomous mission management system offers customers the vision of what their mine could be.
Accuracy, precision keys to digitization drill and blast process
Globally, two certainties face any mine: first, small errors at any stage of the complex drill and blast cycle compound to create costly consequences later; second, declining ore grades mean mines are digging deeper, removing more earth for less ore.
Both challenges call for a tailored drill and blast technology portfolio with seamless data collection at every step. This data-driven feedback loop – enabled by machine learning and artificial intelligence (AI) to automate blast designs and optimize the blast outcome – can be calibrated to increase profit from every blast: drillhole and blast design effectively executed accounting for geology and geometry, using machine-guided, high-precision drills; proven fragmentation analysis and blast monitoring that minimizes loss and dilution.
This holistic pit-to-plant approach addresses the small errors that can compound with costly consequences throughout the complex drill and blast cycle, as well as the sustainability of our resources.
This article supplied by Hexagon AB.
Comments