Electra aims to seize the EV moment: Cobalt sulphate production in late 2022 is just the start of Electra Battery Materials’ plans
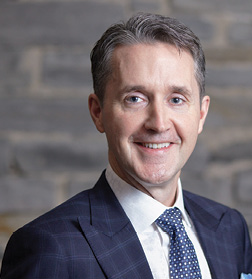
Trent Mell began his career as a Bay Street securities lawyer before leaving the legal profession to work for, not just one or two, but five different mining companies. These days, though, he’s wearing an entirely different hat as president and chief executive officer of Toronto-based Electra Battery Materials Inc. (EBM) – which is in the early stages of developing a vertically-integrated complex to supply North American automakers with the minerals they need to produce battery electric vehicles.
“Hundreds of billions of dollars are being invested to revolutionize personal mobility,” says Mell. “The decarbonization of transportation is a once in a multi-generational moment, not unlike the invention of the internal combustion engine a century ago.”
The company was founded in 2017 and traded under the name First Cobalt, which reflected its original, more limited objectives. The company was primarily interested in finding cobalt assets, either exploration or development projects, that could eventually supply the market with a critical mineral for the decarbonization revolution.
To that end, First Cobalt acquired a conventional silver processing mill in the amalgamated community of Temiskaming Shores that includes the town of Cobalt, Ont., which was at the epicentre of one of the first great Canadian mining booms. “We were going to be the only producer of battery grade cobalt sulphate for the North American market,” says Mell.
Expanding ambitions
From that limited start, the company’s ambitions quickly expanded. A rebranded Electra Battery Materials emerged last November with the vision of producing and supplying to battery makers the suite of chemicals required for the nickel-cobalt-manganese (NCM) batteries currently used in most mid- and high-range electric vehicles.
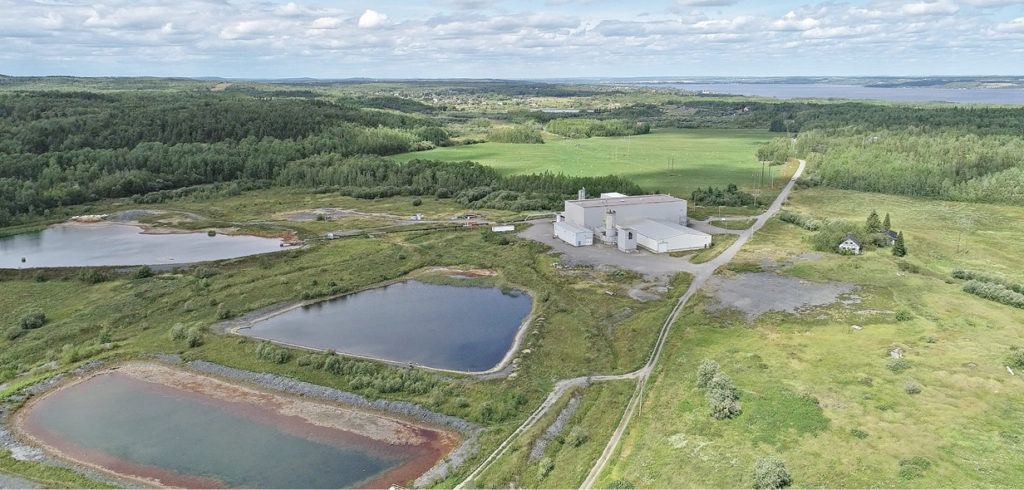
“We’ve got one of the biggest markets in the world south of the border,” says Mell. “We’ve got most of the resources here, but not much attention has been paid to processing the minerals. Our vision is to fill that void.”
The repurposed and expanded silver mill will be used to produce cobalt sulphate, which is the first phase of the company’s four-part plan, and is expected to be operational by year end. EBM has signed agreements with Glencore and the trading arm China Molybdenum to acquire cobalt ore from their mines in the Democratic Republic of the Congo. “It’s a path that comes with some geopolitical risks and environmental social governance concerns,” Mell acknowledges. “To mitigate, that we’re dealing with the biggest and best suppliers. As well, we will be following audit trail and supply train certifications they’ve adopted with OEMs.”
Electra is now targeting production of 6,500 tonnes of cobalt annually (32,500 tonnes cobalt sulphate) – up from 5,000 tonnes (25,000 tonnes cobalt sulphate) because of strong demand for battery-grade cobalt and client feedback.
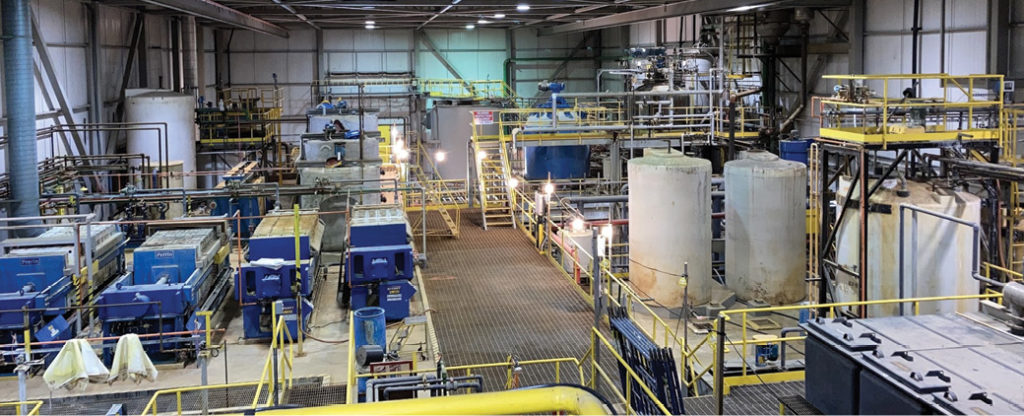
Eventually, EBM hopes to have its own supply of cobalt. The company owns the Iron Creek property in Idaho’s cobalt belt and last June launched an exploration program comprising geophysical surveys, geological mapping and 4,500 metres of drilling. That follows the release in 2019 of an indicated resource for Iron Creek of 2.2 million tonnes grading 0.32% cobalt equivalent, for 12.3 million lb. of cobalt equivalent. It also holds an inferred resource of 2.7 million tonnes, with a grade of 0.28% cobalt equivalent for 12.7 million lb. of cobalt equivalent.
Battery recycling plans
The second phase of EBM’s project involves recovering minerals from used automobile and consumer electronics batteries. The company plans to have a demonstration project up and running within the existing mill this summer.
As Mell explains, recycling companies in Japan, North America and elsewhere strip off the casings then shred batteries to produce a powder called black mass that contains valuable minerals as well as waste products. EBM has contracted with the Japanese conglomerate Marubeni to supply it with black mass, but several North American companies have also expressed interest in supplying the material.
The company will use solvent extraction circuits in the mill to treat the black mass, which involves adding reagents that cause the minerals – a combination of cobalt, nickel, manganese and lithium, depending on the types of batteries – to separate from the waste materials.
The demonstration project will cost upwards of $3 million, but the capital expenditure required to build a recycling plant will depend on how many tonnes per day the company decides to process.
Phases three and four – a nickel sulphate plant and a precursor plant – are at the concept stage. The company is working on commercial documents and technical studies to determine basic parameters such as energy, water and manpower requirements as well as capital expenditures. “In mining terms, it would be more than a scoping study, more the equivalent of a pre-feasibility study,” says Mell.
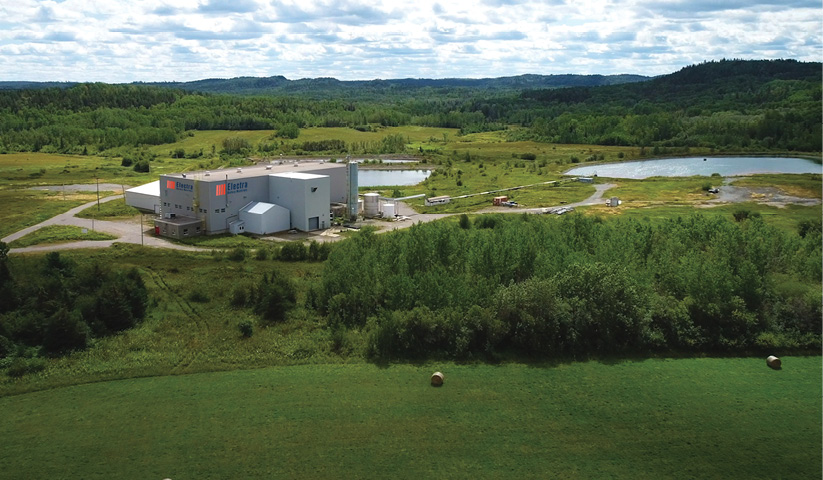
Nevertheless, he projects that both could be built and producing by 2025, though that will involve some significant financing since the nickel sulphate plant will cost between $300 and $400 million to build and commission while the precursor plant will cost in the neighbourhood of $150 million.
There are other hurdles to overcome, one being securing reliable and sufficient supplies of nickel feedstock to keep a plant running. “The problem with nickel is that the stainless steel market is huge,” says Mell. “Nickel sulphate for the battery market is small. It’s something like eight per cent.”
Building and commissioning a precursor plant may be the most complex piece of the project and, Mell says, EBM would likely need to bring in a joint venture or commercial partner. A precursor plant is used to blend nickel sulphate, cobalt sulphate and manganese through complex chemical processes that require the right size particles, the right purity levels and the correct ratios.
‘Huge synergies’
At the same time, there are a number of advantages, one being that EBM would have a vertically-integrated operation that starts with cobalt and nickel ores and ends up with finished products that can be sold to manufacturers of the cathodes used in batteries.
“They’re doing this in China and Finland,” says Mell. “You don’t see it in North America yet. There’s huge synergies that can be captured with integrated refining and precursor manufacturing.”
Apart from the commercial advantages, EBM’s project fits with the Ontario government’s avowed goal of getting the province into the business of producing batteries for the emerging electric vehicle market. The project is also nicely aligned with federal initiatives aimed at reducing greenhouse gas emissions and achieving net zero emissions. And both governments have stepped in with financial support.
EBM received a $5-million interest-free loan from the federal government and a $5 million grant from Ontario. “There’s a growing sophistication at the government level and co-ordination and collaboration with industry,” Mell says. “There are civil servants who get it and are working for us.”
Still, he worries that other countries, especially Australia, are doing more to promote the extraction and processing of minerals critical to decarbonization. Canada is also being held back, he believes, by NIMBYism and our increasingly dragged out, often fractious permitting processes.
“We want to decarbonize, but we don’t want a mine,” Mell says, adding “I know European investors who have shied away from Canada because the permitting regime is too difficult and too long.”
D’Arcy Jenish is an eastern correspondent for CMJ and the author of several books.
Comments
Thomas Flake
I was wondering if this was the same corporation as the Electra mines, corporation during the 1940’s in New Mexico.