How much does innovation add to the cost of water treatment?
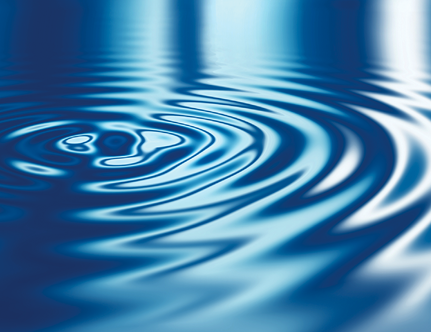
If you attend any mine-related trade show you will notice that there are as many booths displaying products for a variety of water treatment machines and systems as there are for any other single product category. And this emphasis is justified. Water quality is an ever-expanding issue as the developing world catches up with standards currently in place in Canada, the United States, Western Europe, and Australia. All these new methods, systems, and machines come with an associated cost, and it is worth trying to understand who pays for the innovation and how much it adds to overall mineral development expenses.
Why is this an issue for the mining industry? It is critical to understand that the prices for precious and base metals are fixed. They cannot be increased by mineral producers to cover the costs of innovation. In contrast, industries like aerospace, pharmaceutical, automobile, and energy can pass research and development costs directly to those who may benefit. For those developing mineral deposits, increases in costs directly impact profit (or loss).
In the pharmaceutical industry, the final price of a new product to the consumer can be based to a great extent on the research behind it, and as such this price covers to a large degree the costs of development and innovation. The aerospace industry is a little different in that production costs are typically where most of the dollars are spent, so the costs of innovation to the client are not so severe. Still, the client bears these costs.
How much does innovation in water treatment impact the mining industry? There are a variety of factors that shape the answer to this question. For example, companies that develop treatment processes have clients outside the mineral industry. Public utilities, food processing plants, and manufacturing facilities all fall into this category. Public utilities can increase their revenues through a variety of measures to cover the costs incurred for research and development. But because mining companies pay the same as public utilities for these methods and systems, there is an internal economic burden that mining companies face without realizing a similar benefit.
Water treatment research for public utilities and food processors centre primarily on the elimination of dangerous pathogens, although heavy metals and acidity can also be an issue. In the mineral processing industry, it is most often the deleterious elements and the level of acidity that are concerns. So a good deal of the costs of innovation in municipal water treatment, while they may in part be borne by mining companies, are not designed for our needs. Still, it is difficult to know whether the dispersal of the costs of innovation through clients external to the mining industry is a hindrance, or a help.
On the other hand, it is also critical to note that while the capital costs associated with innovation are of concern, at least some of this research, engineering, and machinery development goes into designing very low-cost treatment options. This can be attributed to the fact that so much water contamination is found in areas where the funds, infrastructure, and regulations are not yet in place to ensure clean water. For instance, an estimated 100 million people in developing countries today are exposed to excessive levels of arsenic in their water. Typically, the costs of the more elaborate purification methods used in North America are out of reach of those tasked with providing safe drinking water in these regions. However, Monmouth University chemistry professor Tsanangurayi Tongesayi has developed an inexpensive system that uses chopped up pieces of plastic beverage bottles coated with cysteine (an amino acid) to remove arsenic. As reported by the American Chemical Society, the solution has been able to reduce arsenic levels from 20 parts per billion (ppb) to 0.2 ppb in tests – a level that meets the US. Environmental Protection Agency’s standard.
This research provides a low-cost, practical alternative. It serves as an example of an investment in research and innovation that results in a positive impact on both water quality and profitability for remote mineral development projects.
Diminishing returns?
An argument can be (and has been) made that innovation in the treatment of mine effluent may have reached a point of diminishing returns. It is simply a fact that the water draining from many sites is cleaner now that it was prior to mine development. The Red Dog project in Alaska is a prime example. Because so many mine sites were initially developed long before water quality base-line studies were the norm, it is not necessarily correct to say that mineral development is always the problem. So, at issue here are the standards; are mine developers responsible for making the water cleaner than it was originally? Regardless, while water treatment can no longer be considered a new field of endeavor, it is still one that is ripe for expansion and innovation.
Revenue generation
Our focus to this point has been the costs of purification. In many parts of the world water is extremely scarce and the return of plant process effluent and mine wastewater to a useable form can represent a revenue stream, as opposed to an expense. A process which combines reverse osmosis and de-ionization has been introduced to mines in remote areas with little access to fresh water. It cleans contaminated water in situations where recycling is critical for sustainability. According to the manufacturer, the process results in water quality suitable for crop irrigation adjacent to mines, which could be “quite lucrative” with bulk water valued at roughly $4,000 per million litres.
In addition, new technology also exists that can accurately measure evaporation rates and reduce evaporation by up to 90%. As reported by Venture Magazine, this can save money on financial assurance bonds that often overestimate evaporation rates and reduce the number of new dams that need to be built.With all these factors in play, it is nearly impossible (and perhaps misleading) to try to gauge the real impact of the costs of innovation on the minerals industry. However, some insight is possible. A brief survey of the purchase prices for machinery designed specifically for water treatment in Costmine’s Reclamation Cost Service shows an average increase of roughly 47% from 2011 to 2021. For instance, a 375 litre-per-minute capacity reverse osmosis plant that was reported to cost US$110,300 in 2011 today is listed at US$162,100. According to the U.S. Department of Labor, Bureau of Statistics, the average purchase price for machinery in general increased roughly 22% over that same time period. It is of course presumptuous to say that the difference in cost increases between water treatment machinery and machinery in general is attributable to focused innovation. It is also unlikely that the sampling from Costmine is fully representative of the water treatment machinery industry. But water treatment is a growing field with a high demand for treatment options and it is certain that funds are spent designing and researching innovative techniques.
While there is obviously a cost associated with the research, development, and of newly imagined methods of transforming mine wastewater to a standard equal, or superior, to its original state, at first glance it appears as though these costs do impact the profitability of mineral development projects, although perhaps not significantly. The fact that many are designed to reduce the long-term operating costs in a way that may generate revenues and that at least some of the research and development expenditures can be shared by larger associated markets keep the expense of providing clean, usable water well within reason.
Scott Stebbins, P.E., is president of Aventurine Mine Cost Engineering and can be reached at aventsherp@aol.com. He is also a principal consultant at Costmine (www.costmine.com).
Comments