Sustainability in sight for mining

How new solutions in equipment and technology are lowering GHGs and changing the future of mining
Sustainable mining may seem like a contradiction, but more and more mining companies are looking at solutions to reduce their impact on the environment.
In 2020 the World Bank stated that in order to meet the Paris Agreement targets, ambitious climate action will require a large-scale transition to clean energy which will drive significant demand for minerals (see the World Bank’s Minerals for Climate Action: The Mineral Intensity of the Clean Energy Transition report). This presents Canada with an opportunity to be a leading supplier of responsibly produced minerals and metals to help the country transition to a low carbon economy.
There is no one size fits all solution for a climate plan. Each company, region and country has unique needs and requirements depending on where they sit on the sustainability scale. One of the biggest misconceptions is that sustainability has to come at the expense of productivity. The reality is that innovations in equipment and technology can drive productivity, reduce costs AND decrease emissions.
Setting new targets with equipment, technology and data
The challenge for mining operations is to find solutions that can improve overall sustainability practices, especially as the Canadian government continues to tighten regulations, increase the carbon tax and impose new low-carbon fuel standards. With the introduction of Tier 4 engines, trucks manufactured today are much more fuel efficient than those from 20 years ago. Integrating Tier 4 equipment into your mining fleet is one of the easiest ways to comply with current emissions regulations. However, it’s not going to solve climate change on its own. The potential fuel savings and efficiency is only 2%, with no reduction in CO2 emissions. The development of EPA emission tier standards did not reduce emissions, it only improved the Criteria Air Contaminants. A reduction in emissions means adding another system to the truck which still requires energy (fuel) to function.
Technological advances and sustainable practices provide an opportunity for mining operations to reduce both emissions and their carbon footprint. Using premium equipment not only means greater fuel efficiency but many of these machines can also be rebuilt to their legacy tier emission standard or even a higher value. Rebuilding machines and components at end of life and bringing them back to like-new condition helps reduce overall waste and minimizes the need for raw materials to produce new parts. This keeps non-renewable resources, like equipment, in production for multiple lives, maximizing productivity and reducing equipment costs.
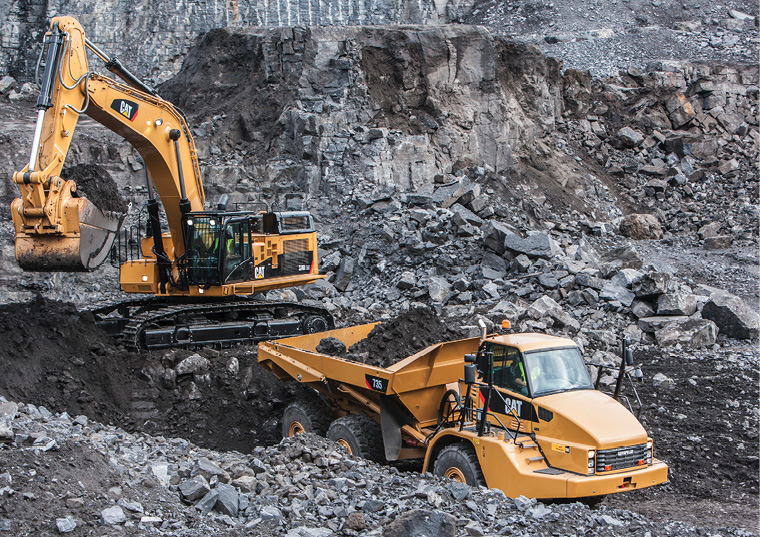
Focusing on productivity is the most impactful way to reduce GHG emissions
In mining, operational optimization and predictive maintenance are critical, but the need to improve energy efficiency and reduce CO2 emissions is equally important. With telematics and data analytics, mines can lower their carbon emissions and find new ways to increase operational efficiencies by leveraging this information. With regular planned maintenance, small problems are found before they become major issues. Repairs can be scheduled at times convenient for the operation, to increase the machines’ availability and maximize uptime. And changing out components before they fail and rebuilding and re-using the worn out parts, can offer substantial savings and reduce waste.
Equipment health data is one of the key contributors to productivity. But sorting through all that data for the information you need can be challenging. Optimizing performance through condition monitoring can unleash the potential for productivity and emissions improvements, maximize equipment usage, eliminate unnecessary hauling, reduce component failures – and help reduce cost per ton.
When you combine condition monitoring with telematics and data analytics, you not only optimize performance but can help predict failures and gather real-time intel for preventative maintenance and predictive equipment analysis. The information that comes from telematics can be used to monitor machine health and condition, track equipment location and hours, emissions and idle time, and optimize workflows, production cycles, and machine uptime.
Leveraging new technologies to drive sustainability
Mining operations face multiple obstacles. They need to dig deeper to reach minerals, and ore reserves are dwindling. Most mines are also in remote locations, so labour and energy costs remain a constant overhead. And now there are added pressures from boards, investors and stakeholders to improve energy efficiency and reduce CO2 emissions while maintaining productivity.
Mine sites operate using the latest technology. Autonomous equipment may not seem like the most direct way to reduce emissions but it provides many benefits that contribute to lower emissions. It reduces idle time, start-stops and fuel consumption, while optimizing acceleration and braking, extending maintenance intervals and maximizing operational hours. Autonomous equipment can also operate 24/7, increasing efficiencies on site and totally eliminating downtime associated with breaks and shift changes.
Electric drive machines are also highly efficient. But switching to electric machines in the mines is no easy feat and there is a long list of variables to consider. Electric drive trucks are quieter and require less maintenance but they also use diesel engines and can burn a similar amount of fuel as a mechanical drive truck under the same hauling conditions. The efficiency of electric drive machines depends on the specific application, overall mine plan and operating condition, which all need to be taken into account to determine the most efficient system for the operation.
Reduce energy costs by increasing the use of renewables
With the emergence of electric car batteries, solar panels and wind turbines, the shift to renewable energy sources is becoming more feasible. But this growing demand for green technologies also presents the challenge of how to source the materials needed to make them. Lithium is needed to produce lithium-ion batteries and rare earth metals are needed for the magnets to produce wind turbines, but mining for these materials in an unsustainable way can further damage the environment. Government policy and regulations are essential to ensure mining activity for renewable energy doesn’t cause more environmental harm than good.

Alternative energy sources could soon become an option for the mining industry. Many alternative energy sources are still in the early stages of development with costs too high to provide any substantial productivity benefits. But they should be carefully considered for future use and planning. Some mine operators are already looking at the benefits of switching to alternative energy sources. One of the most promising solutions currently on the market is dual fuel dynamic gas blending. It uses local resources and can significantly lower fuel costs for mining operations. It also generates less CO2, less NOx content and less total carbon, which can improve the air quality and the long-term sustainability of projects. The lower carbon emissions align with both corporate sustainability strategies and the Canadian government’s clean environment agenda.
There are also future possibilities in switching to Biofuel (B20) which can reduce CO2 by up to 25%. However, today it is in limited supply with typically higher costs compared to diesel due to current production capabilities.
Green hydrogen is another exciting prospect in the industry and will play a key role in helping to decarbonize mining operations. Hydrogen fuel cells for electric vehicles offer big CO2 reductions. They produce zero emissions and deliver the same productivity and performance of diesel. Fuel cells use an electrochemical reaction between ambient oxygen and hydrogen fuel to produce electricity with water vapor and heat as the only byproducts. When hydrogen is sourced from renewable energy using a water-splitting method called electrolysis, the process and resulting fuel is completely renewable. Not only do hydrogen fuel cells eliminate carbon emissions but they also reduce carbon monoxide and particulate matter. This can help improve health and safety conditions in the tight enclosed spaces associated with underground mining.
Hydrogen is not without its challenges – it requires a large capital investment to scale to the supply needed and presents numerous challenges for large mass vehicles, with respect to the energy density, weight tradeoff, charging speed and costs. Despite this, green hydrogen is increasingly being considered and tested in mines with equipment already being built to accommodate the alternate fuel source. In the next several years we could see widespread commercialization of green hydrogen and other sustainable energy sources.
Planning for the future
With so many moving targets given the science, technology and regulatory requirements, not to mention the global nature of the GHG discussion, many companies have already added environmental, social and governance (ESG) experts to their team. This is one of the first steps companies can take for the benefit of employees and customers. The ESG expert can help navigate this complicated topic, keeping on top of sustainability guidelines, grants, funding programs and regulation changes such as the carbon tax.
Mining companies are making progress toward decarbonization, but their focus has primarily been on incremental targets instead of long-term planning for the future. Regulations and technological developments are changing quickly – but we know for certain that reducing GHG emissions needs to be the number one priority. Here are some immediate steps mining companies can take to start making a difference.
1. Set up sustainability leadership committees, or add an ESG expert to your team who can engage with local communities and advocate for environmental issues.
2. Review commodity portfolios, engage with stakeholders and look at the health of your fleet and identify where you can make improvements.
3. Encourage employees and board members to set ambitious emissions targets that will get the company to net-zero and track progress to your goal.
4. Where possible, shift to renewable power generation and invest in energy efficiency projects.
5. Look to actions that will benefit the bottom line while promoting social responsibility.
No longer are the goals of productivity and sustainability mutually exclusive –
technological advancements are allowing both. Aligning sustainability targets with the goal of lowering cost per ton can go hand-in-hand, and as a result it can improve financial performance, reduce maintenance costs and increase equipment productivity for mining operations –
paving the way to a reduction in CO2 emissions and a greener and more sustainable mining industry.
Cayce Kerr is mining industry marketing manager with Finning Canada.
Comments