Keeping costs in check
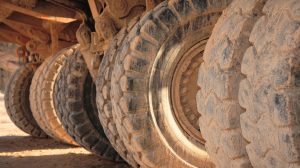
Mining stock image
Understanding your operating costs is crucial to your ability to manage them. Managers should routinely ask themselves questions such as: What are my costs? Which costs have the greatest impact? and Where can I make the biggest difference for my operation’s bottom line?
This article is intended to provide the reader with some context regarding the impact of supply costs on the overall costs of an operation.
When we examine operating costs, we see that they can broadly be categorized into supplies, hourly labour, salaried labour, equipment operation, and miscellaneous. Hourly labour is commonly the largest of these categories, often comprising one-third or more of the total operating cost on a per ton of ore basis. Labour costs, however, are relatively fixed when compared to supply costs and the supplies component of equipment operation. Supply costs can also easily exceed one-third of the total operating cost on a per ton of ore basis, however these costs provide managers with more opportunities to improve their cost structure.
To highlight these relationships, we have studied five surface mine models that were compiled using CostMine’s Sherpa for Surface software application. The models reflect five production rates between 2,000 t/d and 32,000 t/d, and the underlying cost inputs for each of the models are consistent – i.e. for fuel, lube, sundry items, explosives, etc. All models were developed using a 4 to 1 stripping ratio.
Cost Observations
Perhaps the most effective way to illustrate cost relationships is to first consider the broad cost categories outlined in the introduction, followed by more detailed breakdowns of the supply and equipment operation categories. Consider the cost proportions shown in Figure 1.
As one might expect when considering cost line items, Figure 1 shows us that the proportion of equipment operating costs increases with the production level, and the proportion of labour costs diminish with the production level, on a per ton of ore basis. Moreover, we see that miscellaneous cost items remain consistent (these are a fixed percentage of the total operating cost, as per the modelling software used for this study), and supply costs at this high level vary only slightly across the five production levels.
Although informative, the granularity of the cost categories illustrated in Figure 1 is not sufficient to provide a full picture of costs, specifically those related to supplies. For example, equipment operating costs include machine parts, ground engaging tools, fuel, tires, and lube. We see that three of these categories – fuel, tires, and lube – are supply items. As such, we have extracted these to provide the next level of granularity needed to fully understand supply costs (Figure 2). Please note that equipment maintenance labour is considered under the labour category.
Fuel, by a significant margin, carries the largest equipment operating cost for all models, although the observed non-linear cost trend highlights that fleet configurations may also have a significant effect on fuel costs, i.e. equipment types and capacities. Fleet configurations may also be a noteworthy factor with regards to tires, as the proportion of costs allocated to tires increases with fleet capacities.
Figures 1 and 2 tell us that the proportion of operating costs attributable to supplies remains relatively steady across the full spectrum of modelled production rates, however it is important to examine the supply cost breakdown to see where managers may have their greatest impact, regardless of the mine size. Figure 3 shows this final level of granularity for each of the modelled production levels. The figure highlights that the largest contribution to supply costs is the combined ore and waste bulk explosives cost (blasting agents), which contributes between 62% and 77.5% of the total supply cost for the modelled operations. Conversely, we see that blasting accessories (detonating cord, boosters, etc.), drill bits, and drill steel have minimal impact on supply costs, particularly for larger operations.
Discussion
Managers are always looking for inventive ways to cut operating costs. In our view, there are a limited number of approaches that may be of value to an operation:
1. Fleet or plant reconfigurations
2. Personnel reductions
3. Supply cost reductions
Fleet reconfigurations require a significant initial expense and are time consuming. The additional capital outlay requires a life of mine that ensures potential operating cost savings that will eventually surpass capital outlay. While these hurdles may truly be appropriate for some operations, it is generally best that engineers and cost estimators determine the best fleet option prior to mine commissioning.
As discussed above, personnel requirements are usually fixed, both in size and cost. That is, a minimum number of people are required to operate a mine and their wages must conform to that of the region of operation. In our view, personnel reductions are a last-ditch effort to reduce costs in severely struggling mines. One exception would be a personnel reduction due to fleet or plant reconfiguration as per item one above.
Supply cost reductions provide managers with their best opportunity for improving the economics of an operation. Reductions may generally be realized by a) rethinking and reworking mine processes to minimize supply consumption and/or b) direct price negotiations with vendors centred around longer-term contracts and volume discounts. Multiple line item cost reductions may be pursued in tandem, however this article demonstrates that only a handful of supply items generate the bulk of the cost outlay: fuel, tires, and blasting agents. We suggest that it would be beneficial to direct special focus to these. While costs for other items such as drill bits or blasting accessories may be improved upon, their impact on the bottom line will be somewhat marginal. As an example, let us consider fuel and drill bits for the 16,000 t/d production level in this study of surface mines. If we reduced the fuel cost per ton of ore by 10% (initially US$2.16 per ton), the operation sees the benefit of US22¢ per ton of ore, but if we reduce the drill bit cost per ton by 10% (initially US8¢ per ton of ore), the mine would see a benefit of only US0.8¢ per ton of ore.
Without a doubt, controlling supply costs at the mine level can have a significant impact on the profitability of a project and its success. As supported by the example above, each cost centre should be examined for cost savings, recognizing some of these will have a bigger impact on the bottom line than others.
Brad Terhune is a cost analyst and senior geologist with Costmine (www.costmine.com), part of the Glacier Resource Innovation Group, based in Spokane, Wash. He can be reached at bterhune@glacierrig.com or 509-328-8023.
Comments