How tire management can enhance efficiency and lower costs
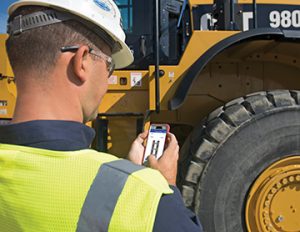
Goodyear’s EMTrack App system offers fast and accurate collection of critical tire data. CREDIT: GOODYEAR TIRE & RUBBER CO.
Tires can be essential to the successful operation of mining equipment and can represent a significant investment for mining operations.
And like any investment, tires should be managed carefully to maintain their performance and generate optimal returns, which can take the form of enhanced equipment performance, downtime prevention and reduced operating costs.
To help mining companies achieve these goals, The Goodyear Tire & Rubber Company has launched a significantly enhanced version of its EMTrack OTR tire performance monitoring system.
“The updated Goodyear EMTrack system enables faster, even more accurate collection of critical tire data like tread depth and inflation levels,” says Eric Matson, global field engineering manager, Goodyear. “It also offers convenient, cloud-based data storage and more robust reporting capabilities thanks to the newly introduced Goodyear EMTrack App.”
Through EMTrack, trained Goodyear tire technicians perform fleet surveys, using a Bluetooth- equipped Goodyear EMTrack scanning tool, to record tire inflation, tread depths and other critical measurements.
Tire performance data then automatically uploads to a cloud-based platform for password- protected storage and easy access. Mining companies can then download captured tire data into easy-to-read, customizable reports that show tire performance.
“Through the Goodyear’s EMTrack, mining company representatives can view collected tire information and reports simultaneously and in real time, regardless of their geographic location, for complete visibility,”
says Matson. “They can view performance data for their tires across their whole operation and even zero in on specific tires, calculating cost-per-hour, cost-per-ton and other key metrics.”
Among other benefits, this can help identify maintenance opportunities to help ensure optimal tire performance. “And the information collected through Goodyear EMTrack can help in forecasting future tire requirements.”
This, in turn, can help mining operations manage their tire budgets more effectively, according to Matson.
“In the mining industry, knowledge is power,” he says. “Our enhanced EMTrack OTR tire performance monitoring system gives end users the information they need to make better decisions about their valuable tire assets.”
Work with an expert
Whether a mining operation is developing a new tire performance management program or is simply implementing measures to improve an existing program, working with a capable tire dealer can have important benefits, Matson notes.
“Select a dealer who has the experience and expertise to evaluate equipment and specific tire needs,” he suggests. “And look for one who can analyze the unique environment in which your machine operates, ranging from underfoot conditions to haul roads that lead into and out of mine sites.
“In addition, a dealer with access to tire performance monitoring systems such as EMTrack can benefit from more robust data to support and enhance its assessments,” Matson adds.
“For example, tread surface conditions, recorded in a performance monitoring system and available to the dealer, can confirm that the right tire has been selected for a specific application, and can even indicate how performance enhancements can be achieved.”
Tire performance data also can help in planning. “By tracking tire performance over time, a mining operation can improve its ability to predict when tires will need to be replaced, which is more important than ever in today’s budget-conscious environment,” he adds.
Matson notes that mining operations can extend the service life of their tires through retreading, in cases where retreads are available for a size and type of tire and are appropriate, based on tire condition. (Goodyear provides mining tire retreading at its facility in North Bay, Ont., and many Goodyear dealers also retread mining tires at their own, independently operated locations.) The ability to retread a mining tire hinges on the condition of its casing. “Following recommended tire maintenance practices – such as regularly checking and, if needed, adjusting inflation pressure levels – can help preserve casing health and integrity.”
Both over- and under-inflation should be avoided. Over-inflation can result in irregular and/or premature tire wear and even a harsher ride for equipment operators. Under-inflation can contribute to irregular wear and increased potential for foreign object damage.
“Under-inflation also can impact a machine’s fuel efficiency since under-inflated tires can force engines to work harder,” says Matson.
While capturing tire data like inflation and tread depth levels, technicians also can look for the presence of other issues, such as cuts and nicks in the tread area, that have the potential to develop into other problems.
They also can check for mismatched tires in size, design and brand. “Mismatched tires can be particularly detrimental to tire life as they may wear unevenly and at different rates,” says Matson.
Findings of this kind also can be entered into Goodyear’s EMTrack system for record-keeping and future reference.
“By understanding the importance of tire management, using a tire management system like Goodyear EMTrack, working with a qualified dealer, and acting upon the data that has been accumulated, a mining operation can help enhance its operational efficiency and reduce its costs,” he says.
This article was provided by The Goodyear Tire & Rubber Company.
Comments