Cold weather maintenance cuts costs and downtime
Canadian mining companies cannot control shifting currencies and commodity prices, but they can control how they operate. There is a real opportunity to increase margins by managing operating assets. A strategic equipment maintenance program helps ensure investments like crushers, shakers, haulers and shovels operate more efficiently and last longer thereby reducing machine repairs or replacement costs, minimizing unplanned maintenance down time and increasing worker safety.
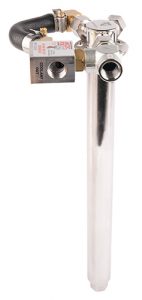
Hot Fox in-tank fuel warmer with thermostat.
By incorporating a rigorous maintenance process that involves maintaining and modifying existing machinery and engaging in preemptive maintenance of new machinery, the industry can drive down costs, increase uptime and prioritize equipment maintenance activities by identifying the behavior of assets or asset components before functional failures occur.
Cold temperatures are another critical factor for many Canadian mines. Mining equipment operates in the harshest environments, which dramatically affects reliability. Although each site’s conditions differ, facing low temperatures, high winds and icy conditions make production difficult at best. Heavy machinery struggle to start and take longer to warm up, and repairs to correct issues caused by cold weather and extreme conditions cost two to six times as much as warm weather fixes.
Fortunately, there are solutions and equipment that mitigate cold weather issues, and the mining industry would be well served to incorporate them into their maintenance programs.
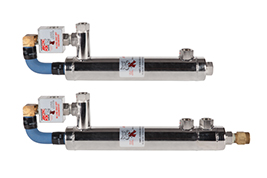
I-909BTEH-B100 in-line fuel warmer with 120V electric preheat.
CREDIT: PHILLIPS & TEMRO
Fuel Gelling
Diesel fuel gels when paraffin in the diesel solidifies due to temperature drops. Of particular interest are two important temperature points: the cloud point (approximately 0 Celsius) which is the temperature at which paraffin wax begins to precipitate in the fuel; and the pour or gel point (approximately -9 Celsius), where so much wax has precipitated that fuel no longer flows.
The solutions are relatively simple, and need to be proactive.
Additives prevent the paraffin wax from gelling together and solidifying. In-line fuel warmers can be installed directly in the fuel line immediately before the filter. This keeps fuel warm prior to entering the filter to avoid clogging. Yet another option is an in-tank warmer which warms fuel as it is being drawn out of the tank. Heat generated from warm coolant is transferred to the cold fuel. If sufficient heat is not available prior to startup, an auxiliary heater can be used in conjunction with in-line and in-tank warmers to preheat the fuel and prevent problems associated with fuel gelling at engine start-up. For larger engine applications or lesser quality fuel, multiple warmers may be used simultaneously.
Cold Hydraulic Fluid
The effects of cold weather are similarly devastating for hydraulic fuels. High oil viscosity can result in a dramatic drop in the the pump’s inlet. The reduction in pressure causes vaporous bubbles which are released into the oil, wreaking havoc on the hydraulic system.
The proactive solution for such potentially affected assets are in-tank warmers, which heat hydraulic fluids prior to equipment operation. Stand-alone heat exchangers transfer excess heat from hot coolant to hydraulic fluid, and don’t require utility power. Subsequently, warm hydraulic fluid reduces pump wear and potential pump cavitation.
Industrial immersion heaters are another option for cold hydraulic fluids. They are electric heaters installed in the hydraulic fluid tank which warms the fluid through direct contact with the heating element, similar to an engine block heater.
Industrial immersion heaters require an AC voltage power supply of 120 VAC or higher, which can be supplied by a gen set or utility power.
Cold Batteries
In deep cold weather, the charge acceptance of batteries is very low, sometimes as low as 2 amps per hour. Keeping the batteries warm will maximize the power output and ability to accept a charge. Additionally, cold electrolyte in a flooded cell battery slows down the molecular action in the battery. The colder the batteries, the more resistant they are to accepting a charge and the available power is decreased.
Maintaining warm batteries before engine startup will help to assure maximum battery power output. During engine operation, maintaining warm batteries will allow them to accept a full charge for engine startup. In cold weather operation discharged batteries can freeze and should not be jumped.
Effective options to maintain battery heat include heat exchangers or electric battery blankets. Heat exchangers installed under the batteries use heat from circulated hot engine coolant. Battery blankets are wrapped around the batteries and run off 120 or 240 Volt AC. These warming products help prevent deep cycling, extend battery life, and put less load on charging systems.
Engine Run Time
Reducing the run times helps extend time intervals between routine service maintenance, thereby reducing the number of hours on the main engine. By adding a preheating system, such as a diesel fired coolant heater or electric heaters powered by a gen set or utility power, the subsequent heat energy sources provide heat to in-line, in-tank or electric heaters without starting the main engine.
Mining operations in Canada rely on heavy machinery which, in many cases, do not have the luxury of operating in optimum conditions. They run in some of the coldest, most adverse conditions and failure is not an option. Granted mining machines are designed to be highly durable, but a proactive maintenance plan and advanced heating systems will ensure they meet the rigorous demands of cold weather, as well as open pit and hard rock mines.
David Marohnic and Vaughn Lenander are sales and application engineers at Phillips and Temro Industries, a global OEM and aftermarket provider of custom engineered thermal systems and solutions.
Comments