Are miners game for virtual reality?
In the lead up to the VRTO (Virtual Reality Toronto) conference in June, exhibitors had the opportunity to explain their innovations to the media, including Canadian Mining Journal. But without simultaneous immersion into the third dimension, some reporters had difficulty grasping the concepts.
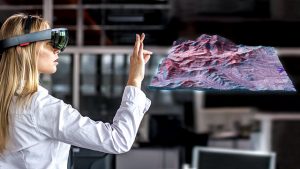
Metavrse’s mining data visualization technology. CREDIT: METAVRSE
Mining engineers and geoscientists face a similar barrier when they present plans to investors, Indigenous groups, or even their own managers. The 3-D reality of exploration and mining does not translate well onto 2-D maps and PowerPoint presentations and vice versa. Without training in 3-D visualization, the human brain struggles to make such dimensional leaps of imagination.
The use of virtual reality (VR) and augmented reality (AR) overcomes this communication challenge by allowing stakeholders to travel to remote exploration and mines sites through a headset. They can lower themselves into a stope, get a bird’s eye view of what a tailings pond will look like in a decade, or immerse themselves in the natural environment of a mine reclaimed.
VR is a computer-generated simulation of a real life environment, whereas AR layers computer-generated enhancements on top of an existing reality in order to make it more meaningful. Both technologies require a headset that costs about $1,200 for VR (e.g. Oculus Rift and HTC Vive, which both must be tethered to a computer) to $5,000 for AR or “Mixed Reality” (e.g. Microsoft’s HoloLens, the first self-contained holographic computer).
“Typically, virtual reality is good for communication and visualizing the future, whereas AR is much more of an operational tool to augment what you are seeing with what you need to do,” says Marni Rabassó, vice-president of Natural Resources at Dassault Systèmes, a French multinational software company that purchased Vancouver-based Gemcom in 2012. Dassault has built a 3-D platform that can connect people and processes during the life cycle of an orebody from exploration to closure.
The first virtual reality head-mounted display system, dubbed the “Sword Of Damocles”, was developed in 1968, but slow processing speeds and the inability to shoot 360° video made the technology impractical. Fifty years later, the headsets remain unrefined – bulky, uncomfortable and frequently sick-making – but they are improving rapidly.
Appetite for disruption
The market for VR and AR is expected to grow to US$80 billion by 2025, according to Goldman Sachs. And costs should fall as the technology becomes more widespread and headsets evolve.
“Miniaturization is coming quickly. All the players are working on it,” says Alan Smithson, CEO and co-founder of MetaVRse, a Toronto agency that provides VR and AR solutions for businesses.
Is the mining industry ready to join the virtual revolution? Although considered a technology laggard relative to other sectors, mining is ripe for disruption after a period of writedowns and poor returns on investment.
“There’s a real appetite for innovation,” says Rabassó. “It’s a big shift for people because it will change the way they work. But the industry is not going back to its ‘bigger is better’ approach.”
Some miners are already experimenting with VR. In 2014 Rio Tinto partnered with Bravo Media to custom design the Oculus Rift to take users on an interactive journey down the Diavik diamond mine in the Northwest Territories. Amec Foster Wheeler offers a similar experience of the K+S Legacy project, a new potash mine in Saskatchewan deigned and built by Amec.
But greater adoption will take time.
“While there is certainly low-hanging fruit in sensors and wireless technologies, fully extracting the potential of Big Data and other next-generation technologies such as three -dimensional virtual reality and simulation will require the development of a rich ecosystem of talent and partners,” says Rick Howes, president and CEO of Dundee Precious Metals.
Howes won the Outstanding Innovator award from the International Mining Technology Hall of Fame in 2016 for marrying different wireless technologies and software systems to provide real time production management and tracking at the Chelopech copper and gold mine in Bulgaria.
That ecosystem is beginning to emerge. Companies such as Dassault and MetaVRse are targeting the mining industry to leverage the technology they have developed for other sectors. And at least one mining engineering consultancy, BGC Engineering, is starting to incorporate AR into its workflow.
Training
Virtual reality is likely to have the biggest impact on job training. Although some mining companies use simulators to train equipment operators, VR tools are less expensive and more versatile. Workers can be trained to handle hazardous situations without having to experience them directly or even be near the site.
“We can transport a full virtual reality system to a training centre where multiple people can train on a particular machine,” Smithson says. “And using data feedback, we can tell if they are paying attention and getting the gist of the training.” Sudbury’s NORCAT, for example, has developed a VR training program using Oculus Rift for Ontario Mine Rescue, the rapid response team for mining incidents.
The program resembles a video game in which team members, through avatars, must work together to manage emergency situations. It could become an invaluable tool for a risky occupation.
In the aerospace industry, Boeing estimates it can reduce training time for aircraft assembly by 75% using the Microsoft Holo-Lens to show engineers how to put different pieces of equipment together. Pop-up text and/or voiceovers would offer the guidance a human trainer traditionally provides.
Communication
Vancouver-based BGC Engineering has recently partnered with Seattle-based LOOOK to improve mining and geoengineering communication using Microsoft’s HoloLens. The consulting firm employs the HoloLens to convey complex 3-D and 4-D information to stakeholders.
“Within five years, this will be a standard part of our workflow,” says Matt Lato, a senior engineer for BGC, which specializes in mine and tailings pond design and closure. “Just as our engineers print off 2-D maps, they will put their designs onto the HoloLens.” The technology will also allow engineers or other experts to be present on the mine or exploration site wherever they may be located. As Smithson points out, it’s impractical and expensive to put a specialized mechanic on a plane to fix a broken machine. But with communication from the remote expert to an onsite employee – both using headsets and seeing the same machine – the repair could be done in minutes at much less cost.
Data Visualization The use of 3-D models in mining is becoming standard practice, but VR could take complex models a step further by allowing people to descend into a mine and jump from level to level or stope to stope, literally immersing themselves in the data without compromising their safety.
“If you have a virtual playground, you can get as crazy as you want without putting people at risk,” says Rabassó. “You can create a world and use it as an environment to imagine what ifs.” Similarly, augmented reality would allow messages to pop up in the corner of a miner’s goggles to, say, warn of unsafe air quality, provide feedback on the stability of a rock face, or give instructions about what to do next. Smithson says research shows workers get more done when they don’t have to interrupt what they are doing to look at their phones or a clipboard for information or instruction.
The mining industry has an opportunity to shake off its reputation as an innovation laggard by incorporating virtual and augmented reality to improve training, com munication, and data visualization. The obvious downside of embracing VR, and new technology in general, is more redundancy as tasks traditionally performed by humans become automated.
How the industry balances this trade-off will determine its performance and reputation in the decades to come.
Comments
Eddie Reeps
This is the Future!!!
a great training tool