Minrail’s new mining system aims at tough-to-mine shallow-angle deposits
Mining shallow-angle deposits – those that lie at between 10° and 45°– has long been a perplexing problem in the mining industry.
While the angle is too steep for mobile equipment on wheels, it’s not steep enough for muck flow. Dilution is hard to control and it can be awkward and difficult to secure the roof with bolts or screens. Typically, the angle results in slow development, low productivity and difficult work flow.
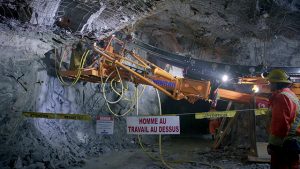
Minrail’s shallow-angle mining system (SAMS). CREDIT: MINRAIL
“Mining in these conditions has always been a nightmare from an engineering point of view,” says Marc Beauvais, a mining engineer with over 25 years of experience and the president and CEO of Minrail. “Gravity is working against you in this situation.”
The “nightmare” is one that’s haunted Beauvais since 2003.
Then working for Aur Resources as a consultant, Beauvais was assigned to investigate mine design for the company’s Duck Pond project in Newfoundland.
The deposit, which varied between 5 and 25 metres in thickness, lay at a 38° angle. Three different mining methods and numerous access drifts were required to access the ore.
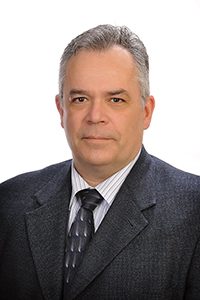
Marc Beauvais.
“I woke up in the middle of the night and I said why not try to find a way to go in at the angle that the orebody is actually resting on,” he said. “That’s literally what happened.”
After investigating existing technologies and ideas, Beauvais found inspiration in a new mining method from a late-1990s R&D project initiated by Société de Recherche et Développement Minier and the Centre de Recherche Industrielle du Québec (CRIQ), tested at the Sigma mine, and then abandoned due to a low gold price. Beauvais spent seven or eight years developing the mining technique and enhancing the equipment before founding Minrail in 2012.
Cousin of the Alimak
Using SAMS, ramp development is the same as conventional mining; it’s stope development that is different.
Minrail’s Shallow-Angle Mining System (SAMS) gets around the difficulties traditional mining techniques have with shallowangle deposits by relying on a central railing that attaches to the roof. The double railing forms the backbone of the system: instead of navigating the slope of the ground with wheels, all the equipment is suspended from the rail.
Beauvais says the technology is a cousin of the Alimak Climber, developed in the 1950s, which similarly works on a monorail mounted on the ceiling. However, the Alimak is mostly for driving raises that are vertical – at 90° down to 50°. “In our case, we go from 10 degrees up to 45 degrees – so this is a range where nobody goes at all.”
Minrail estimates that a two-person crew that’s familiar with the equipment can install the system within 10 hours. The first time it was actually set up in an underground mine (Richmont Mines’ Beaufor), it took about 20 hours with three people to install the railing and mount the equipment.
“This is a big achievement for us, knowing that time is money,” Beauvais says. “If you are going to spend two weeks installing a piece of equipment, right there you’re losing the advantage compared to other techniques.”
Once installed, the system can be operated by one person and can develop stopes that are 12 to 15 metres wide and a minimum of 1.2 metres high.
All of the equipment is electric and modular. This includes the telescopic platform from which the miner controls the system.
SAMS is designed for orebodies up to 6 metres thick to be mined in one pass., Mining cost is in direct relationship with the orebody thickness; as the orebody gets thicker, it gets cheaper to use.
“It’s because the size of the draise is basically the same for an orebody that’s 1.5 metres thick or the one that is 6 metres thick,” Beauvais explains. “So it’s the same preparation work, it’s the same installation time, the same drifting period time. But if you have a stope that’s 15,000 tonnes (of ore) compared to 3,000 tonnes, all the preparation work and cost is diluted.”
Much of the equipment is remotely controlled, and in the future Beauvais expects to automate tasks as well.
Real-mine conditions
Since 2012, Minrail has spent more than $2.3 million investing in the mining method – it’s now patented in Canada and in the U.S.
The company has built prototypes of the equipment, and just this year, SAMS was tested for the first time in an actual mine – Beaufor in Val-d’Or, Que. The mining method at Beaufor is currently long-hole and room and pillar, but Beauvais is hopeful that Richmont could adopt SAMS once the technology is commercial.
A first phase of testing is complete and a second phase could start this summer.
“We found a few glitches here and there, but overall, everything is working as expected. We have to enhance a few things because this is the very first time this equipment is being tested underground, but we’re quite happy with the results.”
An independent report by CanmetMines, part of Natural Resources Canada, outlining the test results will be published sometime in August. Canmet representatives spent time observing SAMS in use and interviewed mine workers about their experience using the system. The results will be presented by Beauvais at the Quebec Mines conference in Quebec City in November.
Productivity boost
When using conventional mining methods on a shallow-angle deposit, it’s difficult to control dilution and secure the roof, Beauvais says.
“Our mining method is highly selective and allows you at any moment to control and keep the integrity of the rock surface to be safe and secure,” he says.
SAMS mechanizes much of the work that in traditional underground mining is done by hand – using long tom drills instead of handheld jack leg drills, for example.
So although the need to install infrastructure adds to development time initially, it reduces development time overall because of its greater productivity, Beauvais says.
SAMS can reduce the underground development that’s necessary to access ore by 40-50%. (A 2012 mine plan for Auriga Gold’s [now Minnova Corp.] Puffy Lake deposit in Manitoba estimated that SAMS would reduce development from 42,000 metres to 26,000 metres.)
While conventional mining methods require vertical separation between levels at every 10-15 to metres, with SAMS, levels are only required every 50 to 60 metres. That means less development in waste rock and a reduction in costs.
Gaining traction
There are several projects in Canada that could benefit from the technology – perhaps half a dozen are assessing their properties and reviewing their mine plans, Beauvais says.
“A lot of deposits have these features of being very difficult to mine because of the resting angle of the deposit.”
Beauvais says mining companies are also having more and more trouble finding and recruiting miners that are capable of “old fashioned” labour intensive mining techniques.
Minrail has met with several companies interested in SAMS and has plans to meet with more.
One thing that has helped get the word out about SAMS was Minrail’s selection as one of 11 semi-finalists chosen out of more than 150 entries at Goldcorp and Integra Gold’s Disrupt Mining competition in March.
“We are very enthusiastic and think that in 2018, we will have something to show to the public,” he says. “We are at the infancy of this technology.”
Comments