How to avoid the cost and risk of a jammed crusher
A foreign object, such as a broken shovel tooth, jamming a crusher presents serious safety issues for any mine. Such incidents can lead to expensive equipment damage and lengthy periods of downtime, bringing operations to a standstill. With the clock ticking, mine personnel must work nervously to remove the obstruction and get the mine working again. Because the huge amounts of stored energy present life-threatening risks, the removal process is potentially the costliest step of all.
Jammed crusher incidents can cause serious injury or even death and can occur at any mine. Canada is no stranger to these tragedies. In 2014, a worker at a mine in Sudbury, Ont., was killed trying to clear a jammed crusher. This fatal incident, which also led to a $1-million fine, is just one local example of the dangers of a jammed crusher. While there are no comprehensive Canadian statistics, American researchers at the National Institute for Occupational Safety and Health found that incidents involving crushers are the second most common cause of fatalities caused by stationary machinery at mines in the United States.
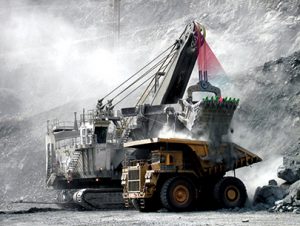
ShovelMetrics
Blockages occur when an object with a higher material strength than what the crusher is designed for enters the crusher. There are many possible metallic or even non-metallic objects that can get caught in a crusher, but some of the most common crusher jam incidents are caused by shovel or loader bucket teeth. When a shovel or loader digs material from a mine face, their bucket teeth have the potential to break off. The problem often goes undetected by the machine operator because of limited visibility in the harsh mining environment. The broken tooth then gets mixed in with the rest of the material and hauled away to the crusher. Since a bucket tooth is made of steel and often weighs over 100 kg, it is too hard for the crusher to break down, causing it to jam.
The tooth removal process is dangerous, costly, and time consuming. First, an excavator needs to dig out all the other material in the crusher, leaving only the obstructing object. Then, a boilermaker uses a torch to heat and cut the tooth in order to loosen it. Because heat causes the metal to expand, the process generates even more pressure than has already been built up, which can cause the 100-kg tooth to shoot out of the crusher at extreme speed.
The best way to avoid a tragedy is to minimize the risk of one occurring. While it is impossible to completely prevent the possibility of broken teeth, it is possible to mitigate the risk of a broken tooth jamming a crusher with safeguards such as Motion Metrics’ ShovelMetrics and LoaderMetrics missing tooth detection systems, currently in use at over 50 mines around the world.
Using a rugged camera with a clear view of the shovel or loader bucket and an on-board computer, the system constantly monitors the bucket teeth as the equipment is in operation. When a missing tooth is detected, the system immediately alerts the operator with an audible alarm and a visual indicator in the in-cab display. The operator can then notify dispatch, and the truck containing the tooth can be routed away from the crusher. The system also sends automatic alerts to MetricsManager Pro, Motion Metrics’ cloud-based data management system, allowing mine management to access critical system alerts.
Shovel and loader teeth do not break off every day and not every jammed crusher results in serious injury or death. However, despite its low probability, a jammed crusher can have a catastrophic impact on mine safety, and on production: If the crusher cannot operate, the entire plant comes to a halt. Therefore, it is imperative for operations to invest in safeguards that can help prevent the unthinkable from happening.
The author is a marketing communications specialist with Motion Metrics International.
Comments