A custom approach to tailings management
There are a multitude of ways to reduce environmental impacts in the mining sector, from extraction, to processing, to waste management, but over the years, the mining sector has been criticized for the environmental impacts of its activities.
In fact, recently we have seen more and more sustainability issues from across the country brought to the public’s attention, putting more pressure on governments to impose and enforce stricter regulations on the mining industry.
Leaders in the industry are making sustainability a priority in their strategies and business models, and one of the many ways mines can become more environmentally sustainable is through creative waste management solutions that can provide tremendous financial and environmental benefits.
But what do I mean by “creative waste management solutions?” Quite simply, it means providing solutions that allow mines to increase performance, safety and efficiency, as well as recover value by processing their waste instead of disposing of it.
The secret is not so much in new technology, but more so in looking at, and using existing technology in creative ways that benefit miners and the environment.
Examples of these include mine slime management, and dredging and dewatering of tailing ponds.
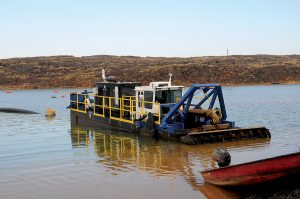
Dredging and dewatering tailings ponds is not a new technology but it`s becoming increasingly
popular as more and more miners look at recycling because of the environmental, and profit factors.
What is dredging and dewatering of tailing ponds?
For decades, mines have been dealing with their waste by disposing of tailings in a pond. Today, the materials in these tailing ponds are seen as valuable and potentially usable. If mines extract them, they can use them. By using standard existing technologies such as dredges, dewatering boxes and centrifuges in different ways, miners are able to recover these materials and recycle them back into the process, or, as raw material. They are essentially brought back to life to become a valuable commodity… not waste.
New regulations requiring that mines clean up and reduce their reliance on tailing ponds have already started to see the light of day. This is only the beginning of what we expect will be much stricter regulations regarding tailing ponds. Mine owners and operators have an opportunity to be proactive and get ahead of the regulations by creatively employing these existing technologies to help solve their environmental challenges.
What is mine slime management?
Most underground mines use water for drilling, cutting, washing and dust control. This water, in addition to the normal seepage of groundwater, flows to underground holding sumps. Over time, fine rock cuttings, dust and sand build up in the sumps, eventually decreasing their holding capacity for mine wastewater, and needed to be cleaned.
The traditional approach to managing underground slimes is costly and time-consuming. It involves allowing the solids to settle to the bottom of the sump while the cleaner water from the top flows over to a clean water sump. The harder, thicker slimes are typically cleaned out using scoop tram equipment and transported to a vacant area in the mine to dewater. The process can take up to six months.
Our company has developed a preventative approach that stops the build-up of mine slime from occurring in the first place. Having already tailored a centrifugation process to manage tailings in the oil sands, we applied this innovative thinking to customize a slime processing solution in the underground mine. This method provides several advantages over the traditional approach: accelerated slime management process; potential metal recovery from slimes; a reduction in equipment repairs and maintenance costs; and improved safety on site.
What are the benefits of these environmental solutions? From mine slime management, to dredging and dewatering, the environmental solutions are advantageous to the mining industry for a variety of reasons:
1 Value Recovery: Instead of disposing of it, processing waste through dredging and dewatering allows mines to recover minerals that can be reused in the mine’s processes.
2 Environmental Performance: At the end of the day, these solutions are turning waste into raw material and products. It has never been more crucial for companies in the mining sector to abide by increasingly stricter environmental regulations, and go above and beyond compliance to build profile as sustainability leaders.
3 Cost Savings: More often than not, our environmental solutions enable mines to recover and reuse enough product to cover the costs of the services, and then some.
4 Convenience: By bringing solutions onsite to mining locations, we are providing customers with a safe, convenient, turn-key approach to managing and processing their waste onsite.
To conclude, the truth is, the mining industry needs to keep pace with sustainability requirements, and most importantly, the changing regulatory and compliance environment.
Soon, the industry will be not only encouraged but compelled to revisit the current way they do things and switch to solutions that are more environmentally friendly. The fact that these environmental solutions are hands-down better and often more cost-effective than current services makes adopting them sooner rather than later a virtual no-brainer.
Information for this Special Report provided by Todd Smith, Vice-president, Environmental Solutions – Onsite, Terrapure.
Comments